Using 3D printing, additive manufacturing, and conventional methods, rapid tooling (RT) accelerates tool, mold, and component manufacture. quick tooling decreases development time and costs, enabling industry compete in quick markets.
Rapid Tooling Knowledge
Rapid tooling produces molds, dies, and other production equipment quickly. Traditional machining takes weeks or months for these tools. Rapid tooling uses 3D printing, CAD, and CAM to save time.
Rapid tooling manufactures mass-production tools quickly and inexpensively, spanning prototype and full-scale manufacturing. Rapid tooling doesn’t need expensive materials or post-processing, making it ideal for short-run production or design concept testing.
Rapid Tooling Types
Direct and indirect rapid tooling are the main types.
- Direct quick tooling: CAD data is used to create tooling components without intermediary stages. SLS and stereolithography are used for this. Direct fast tooling is great for prototyping or building functional components to verify form, fit, and function before mass production.
- Indirect Rapid Tooling: A model or prototype is utilized to make the final tool. A 3D-printed object is often used as a master template for casting or other molds. This approach is often employed when the finished tool needs more robust or particular materials than direct 3D printing.
Both approaches have benefits based on design complexity, material needs, and manufacturing quantities.
Key Rapid Tooling Technologies
Rapid tooling uses numerous modern technologies to improve productivity and accuracy. The fast tooling revolution is driven by several technologies:
Rapid tooling requires additive manufacturing technologies like SLS, SLA, and FDM. These technologies can directly create complicated shapes that conventional machining cannot.
CAD software lets designers and engineers create complex tooling component models for accuracy and practicality. No intermediary drawings or templates are needed to control machines in additive and subtractive manufacturing using CAD data.
Rapid tooling may entail CNC machining, which removes material from a solid block to form it. When paired with 3D printing, hybrid techniques may make tools faster and cheaper.
In indirect fast tooling, 3D-printed patterns are used to make molds for casting polymers, metals, and ceramics.
Benefits of Rapid Tooling
Rapid tooling has several advantages, making it popular across industries:
The considerable decrease in manufacturing time is a major benefit. Rapid tooling allows organizations to adapt faster to market needs than traditional tooling, which may take weeks or months.
Rapid tooling reduces tool production time and materials, saving producers money. This helps with small production runs or prototyping, when standard tooling may be too expensive.
Flexible Design: Rapid tooling allows complicated and detailed designs that traditional techniques cannot create. Designers may swiftly tweak prototypes without expensive retooling.
Rapid tooling works with plastics, metals, and composites. This versatility lets producers pick the optimum material for lightweight prototypes or strong production equipment.
Rapid tooling improves production sustainability by utilizing fewer raw materials and decreasing waste. Additive manufacturing utilizes material just when required, reducing waste.
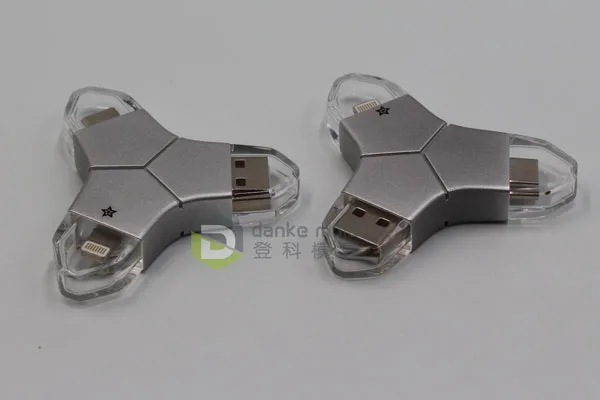
Phone chargers
Applications of Rapid Tooling
Rapid tooling is useful in many sectors. Its speed in making unique, accurate instruments makes it important in fields like:
Automotive Industry: Rapid tooling creates vehicle component molds and prototypes for quicker design iterations and testing. Motorsports benefit from quick prototyping, which improves performance in record time.
Rapid tooling helps aerospace manufacturers make lightweight, high-strength aircraft and spacecraft parts. Rapid tooling creates unique components without sacrificing performance or safety.
Rapid tooling helps medical device producers design and test surgical instruments, prostheses, and other components fast. Creating patient-specific tools is crucial in this market.
Consumer electronics: Rapid tooling speeds up product development and manufacturing in consumer electronics, where innovation advances swiftly.
The Future of Rapid Tooling
Rapid tooling technology will enable even greater production advances. Additive manufacturing, better materials, and smarter software will speed up, simplify, and lower tooling costs. Rapid tooling will improve if AI and machine learning are integrated into manufacturing processes to enhance design and production.
Conclusion
Rapid tooling is changing manufacturing by lowering lead times, prices, and design and production flexibility. As technology advances, quick tooling will shape manufacturing processes and help organizations stay nimble and competitive in a fast-paced market.