Injection molding is a complex manufacturing technique in which a special hydraulic or electric equipment melts, injects, and sets plastic into a metal mold to form it.
Plastic injection molding is the most common technique for producing components because:
- Flexibility: Manufacturers may tailor the mold design and plastic-type for each item. This enables the manufacturing of both basic and complicated designs.
- Efficiency: Once set up, injection molding machines can create huge quantities fast. Electric devices also improve energy efficiency.
- Consistency: When parameters are tightly managed – the process produces thousands of identical components with consistent quality.
- Cost-effectiveness: Although the mold is the most expensive, the cost per component is minimal when made in large quantities.
- Quality: Injection molding can produce – sturdy, detailed, and high-quality – components repeatedly.
Because of these advantages – speed, affordability, and quality – injection molding is the preferred method for producing components in a wide range of sectors.
So, how does it work?
To achieve high-quality plastic products, the injection molding process requires careful control over several variables. Understanding how this process works assists manufacturers in locating dependable producers capable of delivering the required quality and consistency.
Step 1: Choosing the proper thermoplastic and mold
Before beginning the injection molding process – it is critical to choose the appropriate thermoplastic and mold since they form the finished pieces. Manufacturers must ensure that the plastic and mold function well together – since certain polymers are not suitable for specific mold designs.
Each mold consists of two parts – the cavity and the core. The cavity – is a permanent component into which the plastic is injected. And the core – moves into the cavity to produce the final shape. Molds may be designed for single or many pieces. Molds are often built of – steel or aluminum -because of the constant exposure to high pressure and heat.
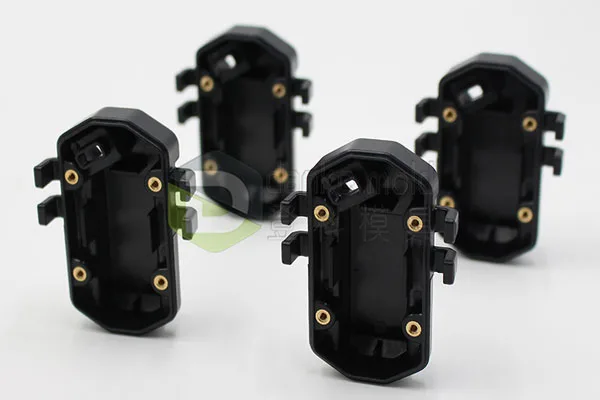
Plastic products
Step 2: Melting and feeding the thermoplastic
Injection molding machines may use either – hydraulic or electric power.
Most machines consist of-
-a hopper,
-a long heated barrel with an injection screw within,
-a gate at the end of the barrel, and
-a mold tool attached to the gate.
Step 3: Adding the plastic to the mold
When the molten plastic reaches the end of the barrel-
-the gate shuts, and the screw returns,
-sucking in a predetermined quantity of plastic and increasing pressure for injection.
At this time, the two parts of the mold are securely closed under tremendous pressure – known as clamp pressure.
Step 4: Waiting and cooling time
After the majority of the plastic has been injected into the mold – it is maintained under pressure for a certain period of time, known as – “holding time.”
Once the holding period is over – the screw pulls back, relieving the pressure. This permits the plastic to cool and firm in the mold, a process known as – “cooling time.”
Step 5: Removal and finishing processes
When the holding and cooling durations are complete, and the component has largely formed – ejector pins or plates force it out of the mold. The component then falls into a chamber or onto a conveyor belt at the bottom of the machine. Once everything is done, the components are ready to be packaged and sent to the makers.