Injection molding makes complex, precise, and durable plastic products. It makes several high-quality, low-waste goods for medical gadgets and vehicle parts. The method, merits, problems, and future of plastic injection molding are addressed here.
Plastic Injection Molding Science
The finished product is ejected after injecting molten plastic into a mold and chilling it. Even complex patterns provide accurate results due to temperature, pressure, and time precision.
Key Process Elements
- Mold Creation: Steel or aluminium molds are custom-made for individual products. They sculpt molten plastic with complex holes and channels.
- Raw Material Selection: Thermoplastics like PP, PC, and ABS are popular, whereas speciality materials are employed for heat resistance or flexibility.
The injection equipment heats and injects plastic, while the clamping device holds the mold firmly.
Process Flow
Plastic pellets enter the machine via a hopper.
A revolving screw melts and homogenises the material.
High-pressure injection: Molten plastic is shot into the mold.
Cooling: The mold cools to solidify the substance.
The final product is expelled, and the process continues.
Plastic Injection Molding Benefits
Manufacturers worldwide use plastic injection molding for its unequalled advantages.
- Accuracy and Repeatability
Tight tolerances provide homogeneity in big production runs using injection molding. For quality-sensitive sectors like aerospace and healthcare, this is crucial.
- Large-Scale Production Cost-Efficiency
Mold creation is costly, but bigger manufacturing quantities lower unit costs.
- Material Flexibility
Manufacturers may pick thermoplastics and thermosets for strength, flexibility, and heat resistance.
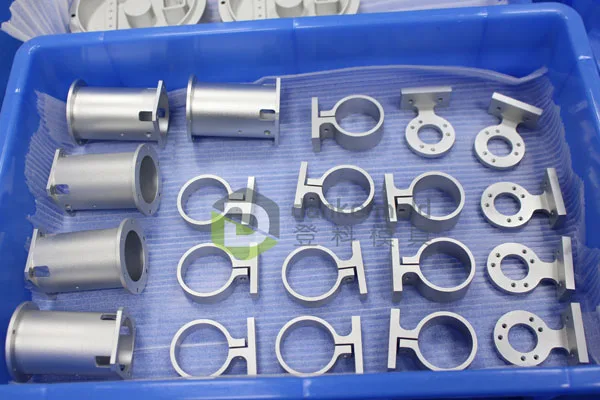
CNC aluminium products
Industrial Plastic Injection Molding Uses
1. Auto Industry
Plastic injection molding is used to make lightweight dashboards, bumpers, and interior trimmings. These components boost fuel economy and design flexibility.
2. Medical Industry
Medical applications need precision and sanitation. Injection molding makes syringes, surgical equipment, and diagnostics.
3. Consumer Tech
Plastic shells for smartphones, laptops, and wearables are usually injection molded for durability and style.
4. Packing Options
Injection molding makes durable, sustainable packaging, caps, and containers.
Challenges in Plastic Injection Molding
Although beneficial, plastic injection molding has drawbacks:
Mold design and manufacture are expensive.
Material Limitations: Certain polymers perform poorly in certain applications, necessitating careful material selection.
Complexity in Design: The method enables complicated patterns; however, molds may be difficult to make.
Injection Molding Technology Advances
Plastic injection molding is becoming more efficient, sustainable, and adaptable via innovation.
The Smart Molding Machine: Modern machines with IoT sensors monitor temperature, pressure, and cycle times in real time for maximum performance.
Eco-friendly materials and processes: Biodegradable polymers and energy-efficient technology reduce injection molding’s environmental effect.
Hybrid Molding: Mixing injection molding with 3D printing accelerates prototype and enhances design.
Plastic Injection Molding Future
The future of plastic injection molding is green, efficient, and inventive. As industry prioritises sustainability, recycling and biodegradable materials will rise. Technology will improve accuracy and lower labour costs by automating and roboticizing the process.
AI and data analytics will improve quality control by detecting faults and optimising procedures in real time. These advances guarantee plastic injection molding’s survival in a changing industry.
Conclusion
Plastic injection molding underpins contemporary innovation. Its accuracy, productivity, and scalability in producing complex designs have transformed industries. Benefits overcome disadvantages including early expenditures and material choices. Plastic injection molding will shape manufacturing’s future due to technology advances and a focus on sustainability.