Silicone molding is essential to production because it produces intricate, durable items. This adaptable approach meets practical and aesthetic requirements in prototyping, consumer products, and industrial applications. Silicone molding is explained in this article, along with its benefits and impact on many sectors.
Overview of Silicone Molding
Molding silicone rubber perfectly recreates complex forms. This mold is versatile, reusable, and compatible with numerous materials, making it ideal for complex prototypes and mass production. Silicone molding’s adaptability makes it ideal for creative and efficient enterprises.
Silicone Molding Science
This procedure relies on silicone rubber, a polymer with flexibility, heat resistance, and chemical stability. These qualities let it to adapt to different molding procedures, assuring quality and detail in each application. Silicone’s low toxicity and great resistance make it useful in many sectors.
Silicone Molding Techniques
Compression Molding
Compression molding compresses uncured silicone in a warmed mold under pressure. Strong materials like seals and automobile parts are made using this method.
Molding liquid silicone rubber
This innovative technology injects liquid silicone into a mold under regulated settings. Medical and electrical components benefit from LSR molding’s accuracy.
Silicone mold casting
Casting creates copies by pouring resin into a silicone mold for prototype and art. This approach is ideal for delicate patterns and small batches.
Why Silicone Molding?
Greater Flexibility
Flexible silicone molds can capture tiny details that stiff molds cannot. Complex forms and patterns need this flexibility.
High-Temperature Resistance
Silicone can withstand severe heat, making it excellent for automotive, aerospace, and food processing.
Multi-App Safe
Non-toxic food-grade silicone is popular in kitchenware manufacture since it is safe for direct contact with food. However, medical-grade silicone passes biocompatibility guidelines for healthcare devices.
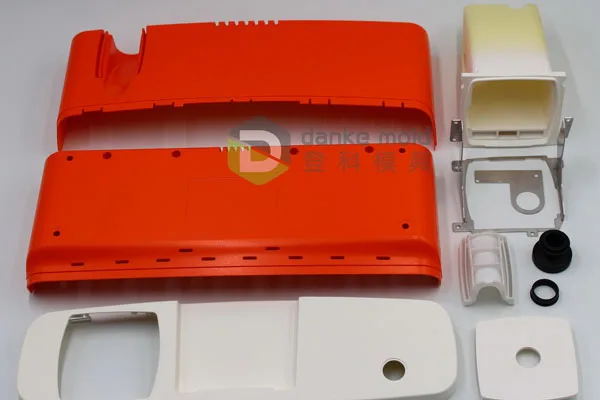
Prototype products
Industry-wide Applications
Medical/Healthcare
Silicone molding is essential for surgical equipment, implants, and wearables. In crucial healthcare settings, its hypoallergenic and biocompatible nature provides safety and dependability.
Consumer Goods
Silicone molding is used in phone covers and bake molds. Consumer goods producers like it because it combines style and function.
Industrial Uses
Industrial silicone molds manufacture mechanically stress-resistant gaskets, seals, and vibration dampeners.
Limitations of Silicone Molding
1. Initial Setup Costs: Custom silicone molds are expensive, which may deter small businesses.
2. Overtime Material Wear: When exposed to abrasive or high-stress materials, silicone molds may degrade.
3. Reduced Size: Small shrinkage while curing affects product dimensions.
Future Silicone Molding Trends
Eco-friendly materials: The industry is using biodegradable silicone to decrease its environmental effect.
Improved Automation: Silicone molding operations are quicker and more accurate thanks to robots and AI, serving high-demand sectors.
Hybrid Manufacturing: Silicone molding and 3D printing enable complex and customisable designs.
Conclusion
Silicone molding’s flexibility, precision, and adaptability make it important to modern manufacturing. Using it in healthcare, consumer items, and aircraft highlights its relevance in contemporary production.
Silicone molding will become more flexible as technology advances and integrates sustainable practices and modern production. Silicone molding can handle current design and manufacturing problems, whether you’re making complex prototypes or high-performance industrial components.