2K injection molding, commonly known as two-shot or dual-material injection molding, is an innovative manufacturing technology that creates components from two materials in one cycle. This method is flexible and may generate parts with softness, durability, and color. 2K injection molding improves product functioning, aesthetics, and assembly costs, making it popular across sectors. 2K injection molding fundamentals, benefits, applications, and obstacles are covered in this article.
What’s 2K injection molding?
2K injection molding creates a multi-material object by injecting two materials into a mold in two phases. Two injection units mold the first and second materials sequentially. These materials may be various plastics or rubber or elastomers.
The item features a rigid exterior and a squishy, rubber-like inside. Applications that need shock absorption, flexibility, or increased grip without extra assembling stages benefit from this method.
Two-K Injection Molding
The 2K injection molding method has many crucial phases that guarantee both materials are effectively merged into the finished part:
1. Mold Design
Mold design is crucial to 2K injection molding performance. Molds have several cavities and cores to retain various materials throughout injection cycles. Proper adhesion and molding need consideration of material parameters including viscosity and cure time.
2. Injection Cycle One
First, material is pumped into the mold. The foundation or structural section of the component may be stiff plastic. The mold moves for the second injection after the initial material is injected and halfway cooled.
3. Second Injection
Once the first material solidifies, the second is pumped into the mold. This softer or more flexible substance, such thermoplastic elastomer (TPE), binds to the first as it cools. The second material may be injected directly onto the first without a gap or layer, allowing for seamless material integration.
4. Cooling/Ejection
The portion cools fully after the second material is injected and solidified. The mold opens and ejects the final item after cooling. The two materials will bind, forming a multi-material component.
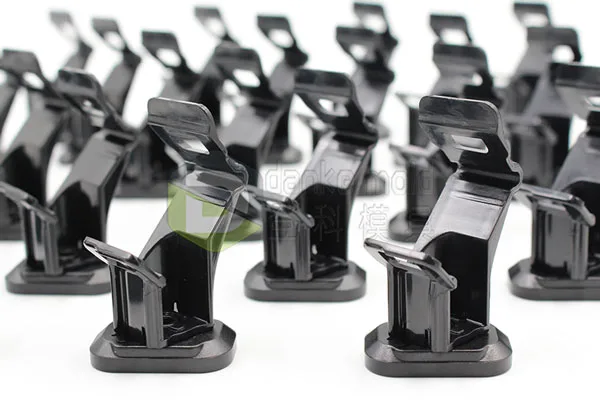
Custom plastic parts
Advantages of 2K Injection Molding
2K injection molding has several advantages over single-material injection molding. Key benefits include:
- Improved Product Function
Manufacturers may mix the finest qualities of two materials in one component. For durability, the exterior layer may be hard plastic, while the inner layer could be soft for comfort or flexibility. Innovative items with better functionality are possible.
- Lower Assembly Costs
Traditional multi-material components required separate production and assembly operations. Both materials are manufactured in one shot using 2K injection molding, eliminating assembly. This cuts labor costs, boosts efficiency, and simplifies manufacturing.
- Better Looks
2K injection molding lets producers make components with numerous colors or textures, improving product aesthetics. This is beneficial for consumer items, automobile interiors, and other appearance-sensitive products.
- Greater Durability
2K injection-molded multi-material components are more durable than single-material ones. Parts may be lightweight and sturdy or resistant to chemicals, severe temperatures, and physical wear by combining materials.
- Design Flexibility
Manufacturers have more design options when using multiple materials with diverse qualities. It lets them make items with more complicated geometries and better performance than single-material molding.
Conclusion
2K injection molding is a cutting-edge method for making complicated, multi-material components in one cycle. With its capacity to blend the greatest qualities of diverse materials, 2K injection molding is changing automotive, electronics, and medical device sectors. Its greater usefulness, attractiveness, and lower assembly costs help manufacturers satisfy current consumer and industry needs.