In the intricate world of vacuum casting, where precision and detail are not just important, but paramount, silicone mold-making plays a pivotal role in unlocking high-quality and accurate parts. The silicone mold, serving as the foundation for the casting process, directly influences the final product’s fidelity and overall success. Therefore, mastering the intricacies of silicone mold making is not just essential, but a key to achieving exceptional results in vacuum casting.
The Silicone Mold Making Process Demystified
Silicone mold making involves a series of carefully orchestrated steps, each playing a crucial role in creating a mold that captures the finest details of the master pattern. Let’s delve into the key stages of this process:
- The journey begins with meticulous mold design, considering factors such as part geometry, undercuts, and venting requirements. The master pattern, often 3D printed or CNC machined, is the cornerstone of this process, meticulously prepared to ensure a smooth and blemish-free surface for mold creation.
- Choosing the right silicone rubber is not just vital, but a decision that can make or break the mold properties. Factors like hardness, flexibility, tear strength, and heat resistance must be carefully considered, underscoring the need for attention to detail based on the specific application and casting material.
- Mold Construction: The selected silicone rubber is mixed and degassed to remove air bubbles that could compromise mold integrity. It is then poured over the master pattern, ensuring complete coverage and proper venting.
- Curing: Depending on the specific silicone type, the silicone mold is allowed to cure at room temperature or in a controlled environment. Adequate curing time is crucial for achieving optimal mold strength and durability.
Key Considerations for Mold and Part Quality
Several factors influence the quality of silicone molds and the resulting vacuum cast parts. Let’s explore some key considerations:
- Mold Design: Proper mold design, including draft angles, venting, and gating, is critical for ensuring easy demolding, preventing air traps, and achieving uniform resin flow.
- Material Selection: Choosing the right silicone rubber with appropriate hardness, flexibility, and chemical resistance is essential for mold longevity and compatibility with the casting material.
- Degassing: Thorough degassing of the silicone mixture is crucial for eliminating air bubbles that can cause defects in the mold and the final part.
- Curing: Adequate curing time and temperature are vital for achieving optimal mold strength and preventing shrinkage or distortion.
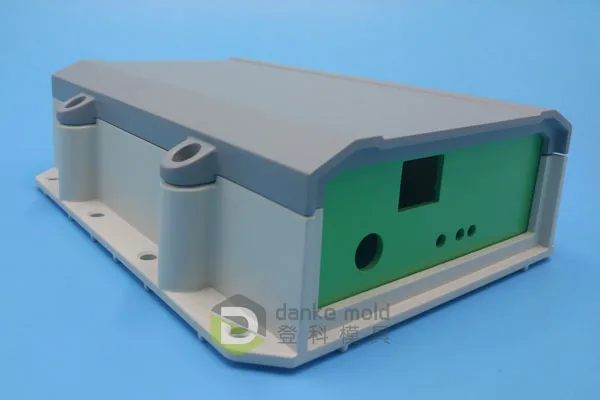
Rapid prototype products
Tips and Best Practices for Success
To achieve optimal results in silicone mold making, consider these tips and best practices:
- Accurate Measurement and Mixing: Precisely measure and mix the silicone components according to the manufacturer’s instructions.
- Proper Pouring: Pour the silicone mixture, it’s crucial to do so slowly and steadily. This careful pouring technique minimizes air entrapment, ensuring a high-quality mold.
- Controlled Curing: Cure the mold in a clean, dust-free environment at the recommended temperature and time.
- Mold Release Application: Apply a mold release agent to facilitate easy demolding and prevent sticking.
- Careful Demolding: Exercise caution to avoid damaging the mold or the cast part.
Troubleshooting and Common Issues
Even with meticulous care, challenges may arise during silicone mold making. Here are some common issues and their solutions:
- Air Bubbles: Ensure thorough degassing the silicone mixture and proper mold venting.
- Incomplete Curing: Verify that the curing time and temperature are adequate.
- Mold Deformation: Choose a silicone rubber with appropriate hardness and ensure proper support during casting.
- Sticking: Apply a mold release agent and ensure proper mold design.
Conclusion
Mastering the art of silicone mold making is fundamental for achieving high-quality vacuum cast parts. By understanding the process’s intricacies, considering key factors, and adhering to best practices, manufacturers can unlock vacuum casting’s full potential and produce parts that meet the most demanding specifications.