In the age of Industry 4.0, manufacturers are rewriting the rules of production. By fusing plastic injection molding with artificial intelligence (AI), companies are revolutionizing product production and achieving unprecedented efficiency, accuracy, and sustainability.
This synergy is reshaping factories and entire industries. Let’s explore how smart manufacturing is pushing the boundaries of plastic injection molding with AI-powered optimization and predictive maintenance.
The Rise of Smart Factories in Plastic Injection Molding
Plastic injection molding, a cornerstone of modern manufacturing, has traditionally relied on precision engineering and skilled technicians. However, the principles of Industry 4.0 are transforming these processes into interconnected, data-driven ecosystems.
Smart factories equipped with AI, sensors, and the Internet of Things (IoT) are no longer constrained by manual oversight. Instead, they leverage real-time data to streamline operations. These systems analyze every step of plastic injection molding, from raw material preparation to final product inspection, ensuring consistent quality and minimal waste.
For example, integrating advanced AI systems with molding machines enables real-time monitoring of cycle times, temperature control, and material flow. This dynamic interaction leads to fewer errors, faster production, and optimized use of resources.
AI-Powered Optimization
AI is at the heart of the shift to smart manufacturing. Here’s how it optimizes plastic injection molding processes:
1. Real-Time Process Monitoring: AI algorithms monitor critical parameters such as mold temperature, pressure, and material viscosity in real time. When deviations are detected, the system can instantly make adjustments, maintaining consistent product quality.
2. Defect Detection and Quality Control: Machine learning models analyze production data to identify patterns that may indicate defects. By catching errors early, manufacturers can reduce waste and rework, saving time and costs.
3. Enhanced Design Capabilities: With AI-powered simulations, engineers can predict how different materials and designs will behave during the molding process. This capability accelerates prototyping and ensures designs are optimized before production begins.
4. Energy Efficiency: AI-driven systems optimize energy use by adjusting machine settings based on production demands. This reduces energy consumption while maintaining productivity.
Predictive Maintenance in Plastic Injection Molding
Downtime is a major cost driver in manufacturing. Traditional maintenance approaches—reactive or scheduled—can be inefficient and disruptive. AI-enabled predictive maintenance offers a proactive solution.
How Predictive Maintenance Works
- Data Collection: Sensors embedded in molding machines continuously collect data on performance metrics such as vibration, temperature, and cycle times.
- Analysis: AI analyzes this data to detect anomalies and predict when components are likely to fail.
- Action: Maintenance is scheduled only when needed, minimizing disruptions and extending equipment life.
By using predictive maintenance in plastic injection molding, manufacturers experience:
- Reduced downtime and increased machine availability.
- Lower maintenance costs by replacing parts before failure.
- Improved safety by identifying potential hazards early.
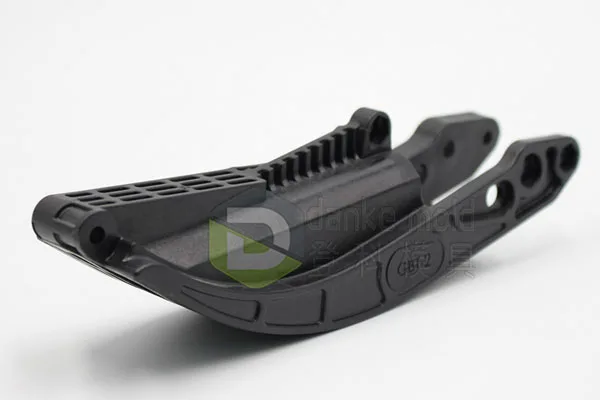
Plastic parts
Key Components of Industry 4.0 in Plastic Injection Molding
The integration of AI into plastic injection molding relies on several core technologies:
- Advanced Sensors and IoT Devices: These devices gather precise, real-time data from every aspect of the molding process. IoT-enabled systems ensure seamless communication between machines and operators.
- Machine Learning Algorithms: AI models analyze historical and real-time data to uncover insights, optimize settings, and predict future trends.
- Robotics and Automation: Collaborative robots (cobots) assist with tasks like material handling and assembly, reducing human error and increasing productivity.
- Cloud Computing: Cloud platforms provide scalable storage and computing power, enabling manufacturers to process vast amounts of data without investing heavily in on-site infrastructure.
Benefits of AI-Driven Plastic Injection Molding
Adopting AI-powered solutions in plastic injection molding delivers significant advantages:
- Improved Product Quality: Consistent monitoring and automatic adjustments reduce defects.
- Higher Efficiency: Shortened cycle times and optimized processes enhance throughput.
- Sustainability: Efficient resource usage minimizes material waste and energy consumption.
- Cost Savings: Lower operating costs due to predictive maintenance and reduced waste.
- Flexibility: AI enables quick adaptation to changing production requirements.
Challenges and Solutions in Smart Manufacturing
While the benefits are clear, transitioning to AI-powered plastic injection molding isn’t without challenges:
1. High Initial Investment
Implementing smart technologies requires significant upfront costs. However, the long-term savings and productivity gains often justify the expense.
2. Data Management
Handling and analyzing large volumes of data can be overwhelming. Cloud computing and robust cybersecurity measures help streamline this process.
3. Workforce Training
Adopting AI and advanced technologies requires a skilled workforce. Training programs ensure employees are prepared to manage and maintain smart systems.
The Future of Plastic Injection Molding in Industry 4.0
As AI and plastic injection molding continue to converge, the possibilities are endless. Future advancements may include self-optimizing machines, enhanced material innovations, and fully autonomous production lines. For manufacturers, embracing these technologies is no longer optional—it’s essential to remain competitive in a rapidly evolving market.
Conclusion
Smart manufacturing is revolutionizing plastic injection molding, with AI-driven optimization and predictive maintenance at its core. By adopting these cutting-edge technologies, manufacturers can achieve unparalleled efficiency, quality, and sustainability. As we move further into the Industry 4.0 era, the integration of AI will continue to reshape manufacturing—delivering better products faster and more efficiently than ever before.