A popular manufacturing technique is plastic injection molding, which involves melting tiny plastic pellets and shaping them into a variety of intricate pieces in big numbers. The production of items we use on a daily basis, such as phone casings, toy pieces, and even automobile components, requires this procedure. This post will outline the principles of plastic injection molding, demonstrate how it works, and emphasize how it differs from 3D printing.
What Are the Basics of Plastic Injection Molding?
Several essential phases are involved in the plastic injection molding process in order to effectively construct complicated parts:
Designing the Product:
Designers plan the item using CAD files according to injection molding specifications. To guarantee quality and moldability, they include elements like draft angles, bosses, and seamless transitions.
Making the Tooling Mold:
Using the design as a guide, knowledgeable machinists make a mold. This mold has elements like sprues, runners, gates, and vents along with the negative form of the component. Its sturdy construction, which includes steel and aluminum, allows it to survive several heating and cooling cycles.
Melting the Plastic Resin Pellets:
By feeding plastic pellets into a machine’s hopper, a revolving screw heats the pellets within a barrel. The pellets maintain constant temperature control by melting into a liquid state without deteriorating.
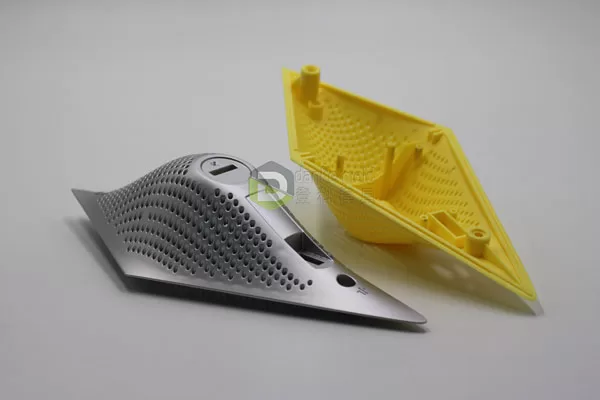
Plastic products
Injecting the Melted Pellets into the Mold:
Melted pellets are pumped into the mold under high pressure using a nozzle to fill the mold cavity all the way to the top and force out any remaining air via vents. This guarantees that the component adopts the precise form of the mold.
The production of commonplace goods, such as electronics and automobile components, depends on the foundational stages of plastic injection molding.
Injection Molding Machine Components
A reciprocating screw, hopper, barrel, heater(s), moveable platen, nozzle, mold, and mold cavity are the parts of an injection molding machine.
Additional details about every injection molding part are in the following list:
Hopper: This is the point of entry for plastic particles into the apparatus.
Barrels: The machine’s outermost component, they contain the reciprocating screw and the plastic grains. The barrel has a heated nozzle at the end and is band-heated.
Reciprocating Screw: As the plastic melts within the barrel, this screw reciprocates back and forth, pushing and compressing the material.
Heaters: By applying heat, these bands cause the solid plastic granules to melt and become liquid.
Moveable Platen: This component exerts pressure and moves to maintain the mold’s two halves’ tight seal. In order to show the completed component, it also releases the mold core.
Nozzle: A heated component that disperses molten plastic into the mold cavity while maintaining a constant pressure and temperature.
Mold: This has the runner channels, vents, and ejector pins in addition to the mold chamber. The mold core on the moving platen and the stationary side next to the barrel make up its two parts.
Mold Cavity: The cavity in the mold where molten plastic is injected to make the finished item, together with any necessary sprues, gates, runners, and supports, is called the mold cavity.