In order to reinforce, improve, and develop a broad variety of goods, plastic components are essential in various industries, including the automotive, home appliance, and medical device sectors.
Since injection molding produces high-quality, dependable plastic components, it is a commonly utilized process. Up to 2028, the injection molded plastics market is anticipated to expand at a 4.6% annual pace.
But even while injection molding can effectively make huge numbers of plastic components, it still needs careful management to guarantee that the finished goods live up to quality requirements. This essay will examine how injection molding works and how knowledgeable producers keep control over the procedure to produce plastic parts of the highest quality.
What is Plastic Injection Molding?
Injection molding is a sophisticated manufacturing technique that involves melting plastic, injecting it into a metal mold, and shaping it into the desired form using electric or hydraulic specialist equipment.
How Does the Plastic Injection Molding Process Work?
Step 1: Picking the Proper Mold and Thermoplastic
It’s important to choose the right thermoplastics and molds before beginning. These components are essential since they dictate the ultimate form and characteristics of the parts. Effective matching of plastics and molds requires careful thought since various kinds of plastics react differently with molds.
The fixed mold cavity and the movable core are the two components that make up mold tools. Because of the high pressures and temperatures involved, they are usually built of sturdy materials like steel or aluminum. Prototyping and testing using computer-aided design (CAD) and 3D printing are often used to modify ideas before final production molds are developed, since developing these molds may be expensive and time-consuming.
Step 2: Thermoplastic Feeding and Melting
Machines for injection molding that run on electricity or hydraulics start by loading raw plastic pellets into a hopper located on top of the apparatus. Whether they are virgin or recycled pellets, they are progressively added to a heated barrel that has a big screw inside of it. The pellets melt into a molten substance that is ready to be injected into the mold as the screw rotates and the barrel warms up.
To guarantee effective injection and perfect molding of the plastic, it is essential to maintain exact temperatures throughout this phase.
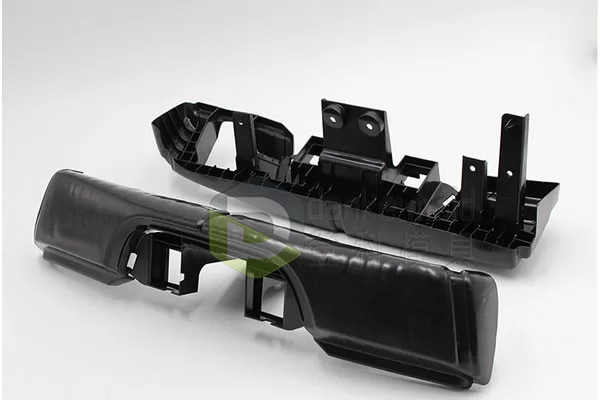
Plastic parts
Step 3: Filling the Mold with Plastic Injection
When the plastic reaches the proper temperature and is molten, the mold shuts firmly under intense pressure. The screw simultaneously forces the molten plastic through a gate and into the mold. Proper injection and clamp pressure balance guarantees proper plastic filling of the mold without leakage.
Step 4: Holding and Cooling
To make sure the plastic fills every crevice of the mold evenly, the mold keeps the plastic under pressure for a certain amount of time after injection. After then, the component cools within the mold (cooling time) and takes on its final form. The kind of plastic and component complexity affect how long these processes take.
Step 5: Procedures for Ejection and Finishing
Extrusion pins or plates force the completed components out of the mold when the mold opens after cooling and solidifying. Prior to being prepared for packing and delivery, these components could go through further finishing procedures, including polishing, dyeing, or eliminating extra material (spurs).
Injection molding generates reliable, premium plastic components for a range of uses thanks to this methodical technique that pays close attention to every detail.