This crucial stage of product development is also known as – prototype tooling or bridge tooling. It makes use of materials like-
-mild steel or aluminum,
-hand-loaded inserts, and
-a common mold base.
Rapid tooling is a – quick and economical – method of component creation. It enables producers to create tools out of low-volume components. Before investing in full-scale production tooling. This technique helps identify and address design defects early on, avoiding problems in the finished product.
It also enables you to use the same materials as in real manufacture. This gives you a better understanding of how your prototype will function in the real world and helps you assess if you have chosen the appropriate materials. For-
-product testing,
-marketing, and
-process design,
rapid tooling is an excellent method of producing small quantities.
So, How Does It Work?
The techniques for creating quick prototype tooling are growing in popularity, along with the need for reasonably priced tooling solutions. There are two primary methods for creating quick molds:
Direct Method
Making the actual mold core and inserts is part of the direct technique. This technique is powerful because – it can produce intricate forms that other techniques may not be able to. For instance, conformal cooling can cut down on cooling time by around 66% by having the cooling channels within the mold match its contour.
Benefits of the Direct Approach
- Fast Production: It just takes a few days or weeks to design and create tools or molds.
- Simple Process: Compared to the indirect method, there are fewer and simpler stages.
- Low Resource Use: One tool or mold may be used to make many prototypes.
- Flexible: It is simple to swiftly alter the design. This approach is an excellent option if you need to test a novel concept. It is also appropriate if your product does not need a lot of description.
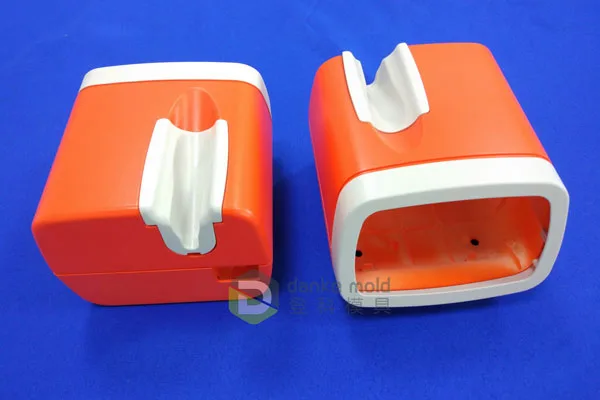
Prototype products
Drawbacks of the Direct Approach
-Not particularly Durable: This process may result in prototypes that are not particularly robust. If you have to change molds often, the low quality of the mold material might result in breakage and increased manufacturing expenses. Making new molds is another need for design modifications.
-Error-Prone: This technique is prone to mistakes, particularly when using various materials, which may alter the proportions of the mold.
The Indirect Method
The indirect method creates the mold or die using a master template in additive manufacturing. This technique often makes use of soft tooling, which creates plastic components using silicone molds.
Benefits of the Indirect Approach
- Sturdy: The materials used to create the master pattern are long-lasting and less prone to break during prototyping.
- Versatile: Depending on the situation, manufacturers can swiftly produce both hard and soft tools.
- Excellent for Testing: This approach enables material experimentation.
Drawbacks of the Indirect Approach
-Time-consuming: Making a master tool requires more stages and takes longer than making a mold the direct way, which raises expenses.
-Not for Easy Designs: For intricate designs that need a great deal of detail, this approach works better. The direct way could work better if your design is straightforward.
How to Pick the Ideal Method for Your Project
Think about the following while choosing a method:
- Budget: How much are you prepared to spend on manufacturing and prototyping?
- Timeline: How soon do you need the finished product or prototype?
- Design Complexity: Does your design need a lot of detail, or is it straightforward?
- Materials: What kind of material will you be using for the product or prototype?