Injection molding is a cornerstone of modern manufacturing, enabling the creation of intricate plastic parts for countless products. However, a critical decision looms for businesses venturing into this realm: should you handle injection molding in-house or outsource it to a specialized provider? This choice can significantly impact your bottom line, product quality, and overall operational efficiency.
In-house injection molding involves investing in your equipment and personnel to manage the entire production process. On the other hand, outsourcing entails partnering with an external company specializing in injection molding services. In this blog post, we’ll delve into the pros and cons of both approaches, providing a balanced analysis to help you determine the best fit for your unique business needs and objectives.
Outsourcing Injection Molding: The Pros and Cons
Outsourcing injection molding offers several compelling advantages. By partnering with specialized providers, businesses gain access to a wealth of expertise and cutting-edge technology that might be inaccessible. This can lead to higher-quality products and more efficient production processes.
Additionally, outsourcing eliminates the need for significant upfront investments in equipment and personnel, resulting in substantial cost savings. The scalability offered by outsourcing is another major benefit, allowing businesses to easily adjust production volumes based on demand fluctuations. Furthermore, by outsourcing injection molding, companies can free up internal resources to focus on their core competencies and strategic initiatives.
However, outsourcing is not without its drawbacks. One notable concern is the reduced control over production processes and quality control. Communication challenges, especially with overseas providers, can lead to misunderstandings and delays.
Intellectual property leaks are also risky, as sensitive designs and technologies are shared with external parties. Moreover, relying on external providers makes businesses vulnerable to supply chain disruptions and potential issues with vendor reliability.
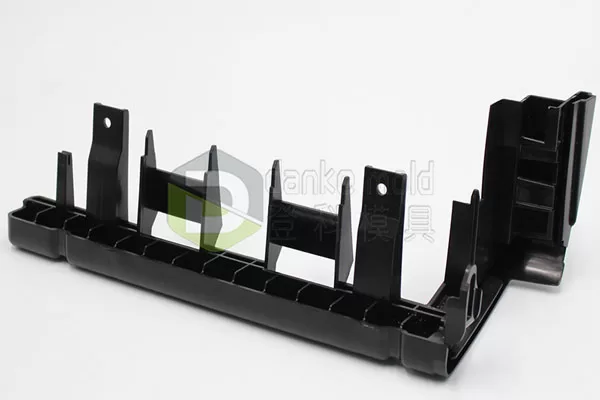
Plastic parts
In-House Injection Molding: The Pros and Cons
In-house injection molding provides businesses with unparalleled control over the entire production process. This direct oversight allows for meticulous quality control, ensuring every product meets exacting standards. Additionally, in-house production can lead to faster turnaround times, as no delays are associated with external communication or logistics. This agility proves particularly valuable when responding to design changes or urgent production needs. Customization is another key advantage, enabling businesses to tailor their products to meet unique specifications or customer preferences. Moreover, maintaining in-house production ensures greater intellectual property protection, safeguarding sensitive designs and technologies.
However, establishing and maintaining an in-house injection molding operation requires a significant upfront investment in specialized equipment, facilities, and skilled labor. This can pose a financial barrier for smaller businesses or those with limited resources. In-house production may also face challenges with scalability, as adjusting to fluctuating demand can be difficult without incurring additional costs.
Furthermore, businesses must factor in ongoing equipment maintenance, repairs, and facility management expenses. Finally, in-house injection molding necessitates specialized knowledge and expertise, either through hiring skilled personnel or investing in training for existing employees.
Choosing the Right Path: Key Considerations
Choosing between outsourcing and in-house injection molding is a strategic decision that hinges on several key factors. Outsourcing offers expertise, cost-efficiency, and scalability, making it a compelling option for businesses seeking to minimize upfront investment and leverage specialized skills.
In-house production, however, provides greater control, faster turnaround times, and the ability to customize, making it attractive for companies that prioritize quality control and flexibility.
To determine the right path for your business, carefully assess your budget and available financial resources for equipment, personnel, and facility management. Evaluate your current and projected production volume, considering whether you need the flexibility to scale up or down quickly. Assess your lead time requirements: do you need rapid turnaround for product development, or can you accommodate longer production cycles?
Determine your customization needs: do you require specific materials, finishes, or intricate designs? Finally, consider your core competencies: does injection molding align with your primary business strengths, or would your resources be better allocated elsewhere?
By thoroughly analyzing these factors, you can make an informed decision that optimizes your injection molding operations and supports your broader business goals.
Conclusion
Ultimately, whether to outsource or keep injection molding in-house is not one-size-fits-all. It hinges on your unique business needs, resources, and strategic objectives. Take the time to carefully assess your situation, weighing the pros and cons of each approach. By understanding the trade-offs and aligning your choice with your specific circumstances, you can confidently decide to optimize your injection molding operations and contribute to your overall business success.