The speed, precision, and cost of plastic injection molding make it popular for component manufacturing. Auto, electronics, consumer, medical, and other industries use it. Pumping molten plastic into a mold hardens it. We cover plastic injection molding’s history, importance, and technology.
Process of Injection Molding
Phases of plastic injection molding are crucial to product quality. Start by making a steel or aluminum mold. Mold has core and cavity. These parts compose the final part.
When ready, little thermoplastic resin pellets are placed in the injection molding machine’s heated barrel. Screws melt pellets as they move. Plastic is injected into the mold under pressure after melting. Plastic hardens after mold filling.
After the component cools, ejector pins remove the finished product from the mold. Mass production is efficient when repeated.
Plastic Injection Molding Benefits
Many features make plastic injection molding a common industrial technology. Component manufacture at low cost and big volume is a major benefit. Mass production becomes cost-effective after mold creation because component prices drop.
The accuracy of the pieces is another benefit. Injection molding offers strict tolerances, making each product practically identical. Automotive and medical device sectors need this precision for accuracy.
Another benefit is material adaptability. Injection molding uses several thermoplastics with variable strengths, flexibility, and durability. This versatility lets producers pick the optimum material for the product.
Additionally, the technique allows design freedom. Proper mold design allows complex geometries, detailed features, and undercuts. This flexibility lets manufacturers make things that are hard or impossible to make otherwise.
Issues and Limitations
Plastic injection molding offers benefits and drawbacks. A major downside is the initial expense of mold creation. Complex molds with several chambers for various pieces may be costly to design and build. Therefore, injection molding is typically uneconomical for low-volume manufacturing.
Controlling the procedure precisely is another difficulty. Temperature, pressure, and cooling time must be monitored and controlled to avoid problems. Warping, sink marks, and inadequate mold filling are injection molding flaws. Quality control must reduce faulty components.
Material selection might be difficult. Plastic melting temperatures, shrinkage rates, and flow properties vary. Choosing the improper material for a component might cause faults or performance concerns. Plastic that shrinks too much while cooling may produce unspecified pieces.
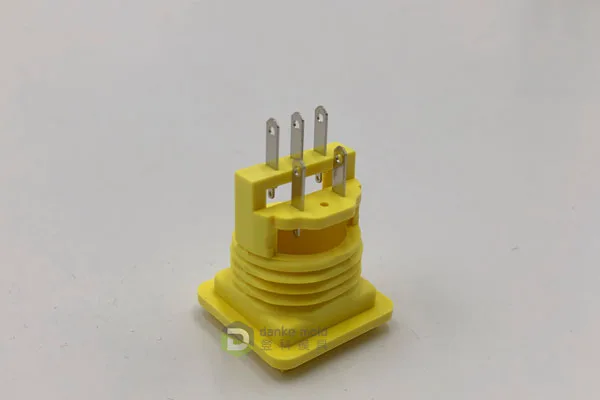
Plastic electrical plugs
Plastic Injection Molding Uses
Many businesses employ plastic injection molding. Car dashboards, bumpers, and door panels are injection molded. Accuracy and durability make plastic components suitable for these applications.
Electronics manufacturers utilize injection molding to make housings, connections, and other tiny parts. Electronics manufacturers need mass-produced lightweight, robust components.
The injection molding process makes syringes and surgical equipment. Its precision and ability to use medical-grade polymers make it popular in medicine.
Plastic bottles and toys are injection-molded. The flexible approach enables makers build items in different shapes, sizes, and colors.
Creative Plastic Injection Molding
Modern technology has altered injection molding. This device makes precise molds using CAD and CAM. 3D printing makes mold prototypes quickly and affordably.
A greener substance is another gain. Injection molding companies employ biodegradable and recyclable polymers to reduce their environmental impact.
Automation is also growing in injection molding. Robotic systems are being used to boost efficiency, save labor costs, and assure quality. Automation is predicted to improve plastic injection molding.
Conclusion
Plastic injection molding has transformed several sectors with its versatility and efficiency. Mass manufacturing uses it because of its accuracy, design flexibility, and low-cost, high-quality components. Modern technology is making plastic injection molding more effective and ecologically friendly, overcoming issues like high mold costs and process control. As industries develop, so will this vital production process.