Almost every consumer product on the market or every industry uses plastic in one way or another. Electronics, consumer products, automotive, healthcare, and even aerospace all use plastic materials to make countless components with a wide range of features and capabilities.
Choosing the plastic material is one of the most crucial processes in any plastic product. Before starting any project, we at Integrated molding solutions evaluate and offer advice on injection molding materials. IMS provides decades of plastics industry experience as a selection guide for materials for plastic injection molding.
Dimensions of the Platen
The table or instrument that retains the mold cavity is called a platen. The mold is placed between the platens and clamped down firmly. The plastic is heated, injected under pressure, and allowed to cool during a molding cooling cycle after the two platens are brought together and kept under tonnage pressure. Here, the plastic assumes its final, hardened shape while still being compressed to a high degree to maintain the desired shape.
Systems for Injection Molding Quality
For the majority of injection molding companies, quality control is crucial. Consumers frequently evaluate businesses based on the goods or gadgets they offer. Every time a defective product hits the market, it becomes difficult to win back the trust of the customer. Injection molding can occasionally be an error-prone process due to its automation.
Part rejection and material waste could occur if a plastic injection molding line problem is not promptly detected. Early identification and resolution of the identified problem(s) is made possible by the implementation of efficient quality control systems. Medical components produced by injection molders certified under ISO 13485 are probably ready for their intended uses.
Tie Bar Distance
The distance on an injection moulding machine between the horizontal tie-bars is called “tie bar spacing”. This measurement basically establishes the largest size of moulds that can be used in the moulding machine, along with the platen max spacing.
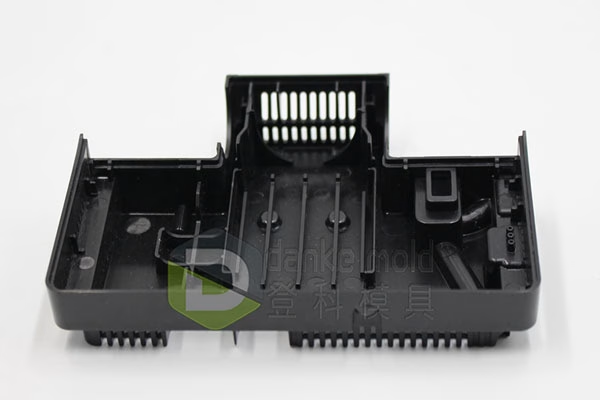
Injection molding parts
Technology and Production Capabilities
Before beginning any project, make sure your molder has the necessary capabilities. Working with a molder who has several presses in different sizes allows them to complete the project using similar materials and colours. To quickly scale production up or down to meet market demand, a partner with the required equipment and cutting-edge technology can assist you, saving you the trouble of finding and qualifying a new contract manufacturer. Time and money can be saved with this kind of adaptability.
- Determine the Size of the Injection Unit
- Knowing this part will help you choose the appropriate unit for your plastic injection molding machine:
- Polymer
- Temporal cycle
- Cooling off period
- Weight of the shot (part weight, weight of the cold runner, and cavity count)
- Maximum injection pressure needed
- Plasticizing rate
- Rate of injection
- Maintain pressure and time.
To ensure high-quality parts are produced, the shot size needs to be determined as a percentage of the injection capacity and should fall between 25% and 65% in order to choose the appropriate assembly.
Snap Size
The best way to describe shot size is as the most plastic that the injection moulding equipment can fit into the moulding cavity in one moulding cycle.
Best practices always dictate that you should look for a machine that can produce shot sizes that are 30–40% larger than what your parts call for.
Write a final note
Selecting the appropriate injection molding machine is crucial because buying one is a significant financial commitment. You can find the specifications of the injection molding machine you require and the injection molding machine manufacturer that is best for you by following the above steps. Every manufacturer will offer a unique remedy. To make sure you receive the product you desire, kindly enquire about all the details with the injection molding machine supplier.