Unlocking the Secrets of Mass Production
Plastic injection molding is fundamental in modern manufacturing, shaping countless everyday products, from toys and electronics to automotive components. This versatile technique has revolutionized the production landscape. But have you ever wondered how it works? Let’s explore the captivating realm of plastic injection molding, breaking down its intricacies for those new to the concept. We’ll delve into the step-by-step process, the types of plastics used, and the wide-ranging applications that make this manufacturing method indispensable today.
What is Plastic Injection Molding?
Plastic injection molding is a manufacturing process that transforms thermoplastic materials into intricate components with exceptional accuracy and consistency. This technique is widely used for mass-producing a diverse range of plastic products, from tiny parts for electronics to large automotive components.
The process begins with raw plastic pellets fed into a heated barrel. The pellets are melted and mixed inside the barrel until they reach a uniform, molten state. This molten plastic, known as the melt, is injected under high pressure into a metal mold. The mold, designed to match the contours of the desired part, shapes and cools the melt, causing it to solidify and take on the mold’s form.
The mold opens once the plastic has solidified, and the newly formed part is ejected. The cycle repeats, allowing for the continuous production of identical parts. The efficiency of plastic injection molding enables the rapid manufacture of large quantities of complex components, making it a preferred method for industries such as automotive, medical, electronics, and consumer goods.
Some primary benefits of plastic injection molding are as follows:
- Achieving High Precision and Consistency: Utilizing molds guarantees accurate reproduction of the intended shape and dimensions, thereby ensuring uniformity and consistency across all parts.
- Complex Geometries: Plastic injection molding can produce intricate parts with complex shapes, undercuts, and fine details, which would be challenging or impossible to achieve with other manufacturing methods.
- High Production Rates: The process’s automated nature allows for rapid production, making it ideal for mass manufacturing.
- Material Versatility: Plastic injection molding can process a wide range of thermoplastic materials, providing engineers with a choice of properties and characteristics to suit specific applications.
- Cost-effectiveness: Plastic injection molding offers a low-pricing solution for large-scale production, as it reduces labor costs and minimizes material waste.
Overall, plastic injection molding is a versatile and efficient manufacturing process that enables the production of complex plastic parts with high quality, precision, and consistency. Its wide range of applications and material compatibility make it a valuable tool in the manufacturing industry.
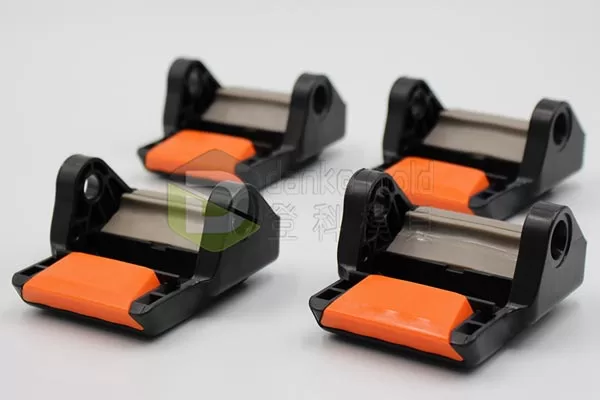
Injection molding products
The Injection Molding Process: Step by Step
- Clamping: The mold comprises two halves and is securely clamped together.
- Injection: Plastic pellets are fed into a heated barrel, melting into a viscous liquid. This molten plastic is then injected under high pressure into the mold cavity.
- Cooling: The plastic inside the mold cools and solidifies, taking the shape of the cavity.
- Ejection: The mold halves open, and ejector pins push the newly formed part out.
- Finishing: Any excess plastic (flash) is trimmed, and the part might undergo additional processes like painting or assembly.
Materials: The Building Blocks of Plastic Injection Molding
The most common plastics used in injection molding are thermoplastics, which can be melted and re-solidified repeatedly. Popular choices include:
- Polyethylene (PE): Used for packaging, containers, and toys.
- Polypropylene (PP): Found in furniture, automotive parts, and medical devices.
- Acrylonitrile Butadiene Styrene (ABS): Commonly used in electronics casings and Lego bricks.
- Polycarbonate (PC): Ideal for lenses, safety helmets, and bulletproof glass.
The choice of material depends on the desired properties of the final product, such as strength, flexibility, or heat resistance.
Common Uses of Plastic Injection Molding
The applications of plastic injection molding are vast and varied, including:
- Consumer Goods: Toys, appliances, kitchenware, electronics casings
- Automotive Industry: Bumpers, dashboards, interior trim
- Medical Devices: Syringes, implants, surgical instruments
- Packaging: Bottles, containers, closures
- Aerospace: Lightweight components and structural parts
In Conclusion
Plastic injection molding is a powerful manufacturing technique that has revolutionized product creation. By understanding the basics of this process, you’ll gain a deeper appreciation for the countless plastic items you encounter daily.
If you’re considering plastic injection molding for your next project, don’t hesitate to contact experts who can guide you. Let’s turn your ideas into reality!