In today’s fast-paced industrial world, speed and efficiency drive digital innovation. Manufacturers can build prototypes and production-ready tools faster and cheaply via rapid tooling (RT). Fast prototyping and standard manufacturing are transforming how firms make products from concept to full-scale production. This article discusses rapid tooling, its advantages, uses, and future influence on manufacturing.
Rapid tooling?
Additive manufacturing (AM) speeds up tool, mold, and die production. Rapid tooling decreases lead times and costs while maintaining functional correctness, unlike weeks- or months-long procedures. The term describes direct and indirect tooling methods that employ speedy prototyping to build production-quality tools.
Direct tooling makes the mold or tool using additive manufacturing. A fast prototype model is used as a master pattern in indirect tooling to cast or produce a mold or die. Quick tooling is helpful in automotive, aerospace, consumer, and medical equipment because to its versatility.
Fast Tooling
Rapid tooling has numerous approaches and technologies, each having benefits depending on the application:
Rapid tooling uses 3D printing. Tooling components are 3D printed using SLS, SLA, or FDM in direct rapid tooling. Layer-by-layer tool building lowers waste and improves precision.
CNC machining: While slower than additive methods, CNC machining may be utilized for quick tooling. It creates high-tolerance molds and dies for low-volume manufacturing. Fast prototyping and CNC machining are used to improve tools before mass production.
In indirect quick tooling, vacuum casting and silicone molding are prevalent. Rapid prototyping creates a master pattern for silicone or other flexible molds. This mold may be used to make several copies of the item for short production runs or functional testing.
Additive manufacturing and injection molding are combined in hybrid tooling. Metal molds may be filled with 3D-printed inserts to decrease tooling costs while preserving strength and longevity. Rapid prototyping and traditional processes are combined for flexibility and dependability.
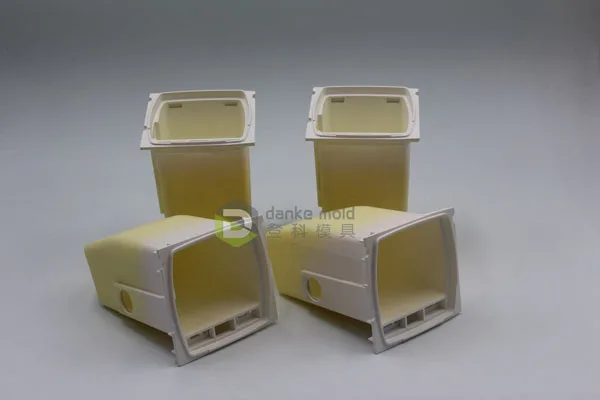
CNC plastics
Rapid Tooling Benefits
Rapid tooling has various benefits over conventional tooling, hence many manufacturers choose it:
- Reduced Lead Time: Tool production time is a major advantage. Rapid prototyping and tooling may speed up product development by days or weeks, whereas traditional tooling might take weeks or months.
- Cost Efficiency: Traditional injection mold tooling requires substantial machining and material, making it expensive. Rapid tooling uses cheaper materials and more efficient production processes for design validation and small-scale manufacturing, lowering these costs.
Rapid tooling adds design flexibility via additive manufacturing. We can create complex geometries, internal details, and elaborate designs that standard tooling cannot.
Iterative prototyping: Rapid tooling lets engineers test several tool or component designs before mass producing them. This flexibility is beneficial in aircraft and medical device production, where design refinement is crucial for performance and safety.
Applications of Rapid Tooling
Rapid tooling has benefits in several industries:
Automotive Industry: Rapid tooling is used to create components for testing and pre-production. Manufacturing functional prototypes with quick tooling speeds up design validation and vehicle launch.
Rapid tooling helps aerospace engineers manufacture lightweight, complicated components fast for accuracy and performance. Creating complex tools using additive manufacturing is very useful for turbine blades, airframes, and other important components.
Medical Devices: Rapid tooling is transforming the medical business by producing specialized surgical equipment, implants, and prostheses quickly. Rapid tooling’s design flexibility benefits medical equipment that must be customized for each patient.
Consumer Goods: Rapid tooling helps consumer goods firms design and test new items as trends shift. Shortening development cycles helps organizations meet market expectations and launch new goods quicker.
The Future of Rapid Tooling
Rapid tooling will transform industries as demand for more efficient, cost-effective, and adaptive manufacturing develops. Improved additive manufacturing technologies like metal 3D printing and multi-material printing will speed up tooling. AI and machine learning will improve quick tooling efficiency and adaptability in design and production.
Conclusion
Rapid tooling has revolutionized production by combining additive manufacturing’s speed and diversity with conventional techniques’ accuracy. Its capacity to cut lead times, prices, and design constraints makes it useful across sectors. Rapid tooling will enable quicker innovation and more efficient production in product development and manufacturing as technology advances.