Project success in the ever-changing industrial business requires time and precision. Rapid tooling (RT) revolutionizes prototype-to-production. By swiftly making molds, dies, and other equipment, rapid tooling accelerates product development. The types, applications, and advantages of fast tooling in modern manufacturing are discussed here.
Rapid tooling?
Rapid tooling makes molds or tooling components from CAD models quickly using contemporary manufacturing technologies. Instead of weeks or months, rapid tooling may shorten lead times to days. It speeds product development by producing prototypes and small quantities of manufacturing components faster.
Rapid tooling is usually associated with additive manufacturing (AM), although it may also involve CNC and hybrid technologies. To save manufacturing time and cost, we create tooling quickly and correctly.
Fast Tool Types
Rapid tooling benefits vary by application. Soft and hard tooling dominate.
1. Soft Tools
Soft tooling makes molds and dies from weaker materials. Their uses include prototyping, limited production runs, and bridge tooling between prototype and final manufacturing. Aluminum, silicone, and urethane are soft tooling materials.
Advantages:
- Rapid and affordable
- Ideal for low-volume manufacture
- Allows cheaper design changes
- Good for functional testing
Disadvantages:
- Limited lifetime due to material wear
- Not good for mass manufacturing.
2. Hard Tooling
Hard tooling uses steel to make molds and dies. It can handle high-volume manufacturing and frequent usage. Despite taking longer and costing more, hard tooling is more durable and precise.
Advantages:
- Long-lasting and accurate
- Suitable for mass manufacture
- Reliable quality for huge runs
Disadvantages:
- Lead times longer than soft tooling
- High startup expenses
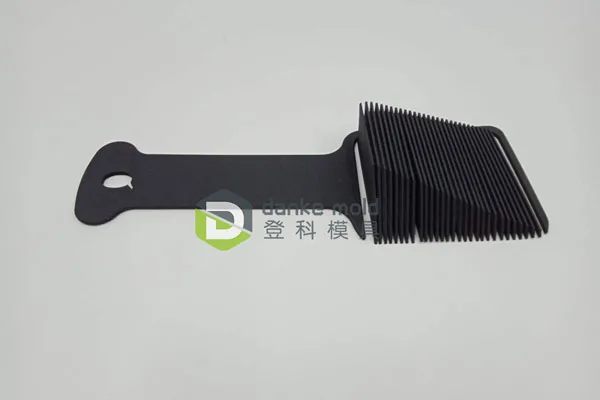
SLS parts
Techniques for Rapid Tooling
Rapid tooling methods vary by material and application. Popular methods include:
3D printing
Rapid tooling is often done via additive manufacturing, or 3D printing. Manufacturers may easily create molds or direct tools for prototype or low-volume production by layering materials from a digital model. SLS, SLA, and FDM are common fast tooling 3D printing technologies.
CNC milling
CNC machining subtracts material from a solid block to form tools. This approach produces precise hard tooling for prototype and large manufacturing.
Hybrid Manufacturing
Hybrid manufacturing makes complicated tools quickly and precisely using additive and subtractive methods. Manufacturers may speed up production and save expenses by combining 3D printing with CNC machining.
Applications of Rapid Tooling
Rapid tooling speeds product development and lowers production costs across sectors. Common uses include:
- Auto Industry : Rapid tooling produces functioning prototypes, bespoke parts, and low-volume manufacturing components for the automobile industry. This lets producers test new designs, make improvements, and launch goods quicker.
- Aircraft Industry: The aircraft industry requires every item to be precise and effective. Rapid tooling lets aerospace businesses make high-quality prototypes, material testing, and small batch production runs, lowering lead times and assuring quality.
- Consumer Goods: Rapid tooling lets consumer product developers evaluate functionality and aesthetics before mass production. This may accelerate product releases and market response.
- Medical Industry: Rapid tooling creates tailored implants, medical equipment, and surgery instruments. Rapid tooling is useful for developing life-saving devices and clinical testing prototypes because to its speed and accuracy.
Rapid Tooling Benefits
Rapid tooling is especially beneficial for sectors that need quick turnaround and high-quality precision products. Key benefits include:
1. Quicker Market Entry
Rapid tooling cuts mold and die creation time, helping manufacturers launch products faster. This benefits sectors with short product lifecycles or fast-changing customer needs.
2. Cost reduction
Rapid tooling reduces manufacturing costs by lowering lead times and early product development hard tooling. Ability to swiftly test and adapt prototypes saves expensive full-scale manufacturing mistakes.
3. Flexibility in Design
Rapid tooling increases design iteration flexibility. Manufacturers may quickly and cheaply alter prototypes or tools to ensure the final product fits standards.
4. Small-batch
Rapid tooling is cost-effective and efficient for low-volume production runs. It makes tiny quantities quickly without costly, high-volume tooling.
Rapid Tooling Challenges and Future
Rapid tooling has pros and cons. For extended production runs, soft tooling may not be sturdy enough, while hard tooling may be too expensive for certain firms. Some quick tooling processes struggle to achieve accuracy and quality in complicated geometries.
Rapid tooling’s future looks bright as technology advances. Rapid tooling may become more efficient and flexible as materials science, 3D printing, and hybrid manufacturing advance. Further development of these technologies will lower prices, enhance accuracy, and broaden quick tooling applications globally.
Conclusion
Rapid tooling is transforming production by lowering lead times and costs. The flexible and efficient solution for prototyping, low-volume production, and full-scale manufacturing streamlines product development cycles across industries. Rapid tooling will become more important in production as technology advances.