A great change is taking place in the manufacturing landscape, driven by the rise of robotics and automation. Robotics and automation are bringing about new production lines that are helping manufacturers realize unprecedented efficiency, quality, and cost-effectiveness. Ready to bring your manufacturing to the next level? It’s time to adopt robotics and automation.
The Rise of Smart Manufacturing
Conventional manufacturing processes that require numerous man-hours are being replaced with an increased focus on automation, which provides tremendous benefits. Robots and automation – their ability to lead to an increase in production and quality of goods – increased output in a shorter time, working with greater precision – much greater than human counterparts. Recent statistics demonstrate the powerful advantages of incorporating robotics in manufacturing:
- Increased Production Output: Robotics-using companies show a positive 35% increase in production output and, therefore, are better able to satisfy increased demand and maintain a competitive advantage.
- Reduced Operating Costs: Automation can significantly reduce operating costs by up to 27%, optimizing resource utilization and minimizing waste.
- Enhanced Product Quality: Robotic systems’ accurate and uniform nature significantly increases product quality by 45%, reducing defects and rework.
- Improved Workplace Safety: Robotics contribute to a safer work environment by taking over dangerous or monotonous tasks. Companies report a 60% reduction in workplace injuries.
Key Technologies Reshaping Production Lines
Several key technologies are driving the automation revolution in manufacturing:
- Collaborative Robots (Cobots): The robots will work hand in hand with humans and will perform repetitive or physically demanding operations while the human worker is concentrating on some of the more complex operations. For example, a top electronics company introduced cobots into their assembly line and cut assembly time by 40 percent.
- Machine Vision Systems: Equipped with smart cameras and AI algorithms, machine vision systems can inspect products and identify defects in real time with exceptional accuracy. An automotive plant implemented automated inspection systems powered by machine vision, reducing quality control costs by 50%.
- Autonomous Mobile Robots (AMRs): These self-driving robots navigate factory floors, transporting materials and finished goods efficiently and safely. One consumer goods company installed AMRs in its warehouse and says it’s been able to double its material handling speed and cut its errors by 90%.
Implementing Automation: A Roadmap to Success
Starting your automation journey requires careful planning and implementation. Here are the methods to get you started:
- Process Mapping: First, thoroughly map out your existing manufacturing processes. What are the steps, and what inputs, outputs, and resources are required for each step?
- Bottleneck Analysis: Analyze your processes to identify bottlenecks or areas where automation could significantly improve efficiency or quality.
- Technology Selection: Choose the best combination of automation technologies to meet your requirements and fit your production environment. Consider factors such as task complexity, the amount of human interaction needed, and budgetary constraints (e.g., total costs).
- Team Training: Invest in training your workforce to operate and maintain the new automated systems. Empower your employees to embrace the technology and adapt to their evolving roles in the automated environment.
- Performance Tracking: Implement systems to track and measure the results of your automation initiatives. Monitor key performance indicators (KPIs) such as production output, quality metrics, and cost savings to assess the effectiveness of your automation strategy.
Success Story: Transforming a Medical Device Manufacturer
A medical device manufacturer facing growing demand and challenges with production consistency turned to automation for a solution. By introducing robotic assembly cells into their production line, they achieved remarkable results:
- Daily output surged from 5,000 to 15,000 units
- Defect rates plummeted by 85%
- Labor costs decreased by 40%
It’s a great story that illustrates the potential of automation to transform the way companies address their production problems.
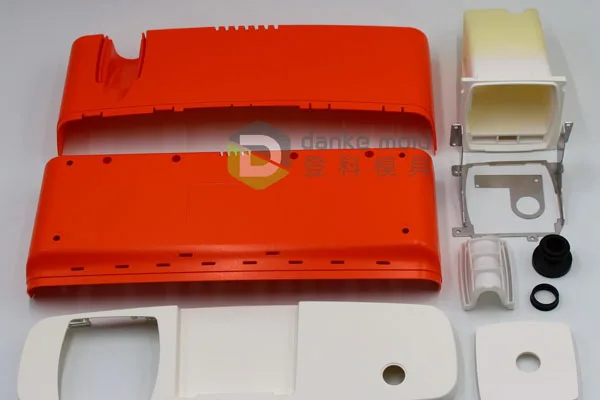
Vacuum casting molds
The Numbers Don’t Lie: The Impact of Automation
Research consistently demonstrates the compelling benefits of automation in high-volume manufacturing environments:
- Uptime: Automated production lines run at an impressive 98% of the time.
- First-Pass Yield: The first-pass yield rate (the percentage of products that pass quality measurements the first time through) is 92% in facilities that use automation, which greatly reduces rework and waste.
- Quality Control Costs: Automation leads to a 75% reduction in quality control costs due to the increased accuracy and efficiency of automated inspection systems.
- Time-to-Market: The ability to automate enables a time-to-market 50% faster by eliminating cumbersome manufacturing processes and reducing lead times, thus providing companies a major edge over the competition.
Charting Your Automation Path
If you’re ready to modernize your production line with robotics and automation, consider these starting points:
- Focus on a Single Process: Start small by automating one process or task. Then, as you gain experience and prove the value of automation, increase the number.
- Define Clear Metrics: Establish clear and measurable success metrics to track the impact of your automation initiatives and ensure they align with your business goals.
- Start Small and Scale Up: Begin with a pilot project and gradually expand your automation efforts as you gain confidence and experience.
- Build on Early Wins: Celebrate early successes and use them to build momentum and gain buy-in from your workforce for further automation initiatives.
Questions to Guide Your Automation Strategy
To identify the most promising areas for automation in your facility, ask yourself these key questions:
- Which processes are most in need of improvement?
- Which tasks cause the most strain or risk of injury for your workers?
- Where are the bottlenecks in your production line?
- Which processes require the highest level of precision and consistency?
Real-World Results: A Packaging Company’s Success
A packaging company struggling with consistency and workplace injuries turned to robotic palletizers to automate their end-of-line packaging process. The results were impressive:
- Throughput increased by 200%
- Workplace injuries were eliminated
- Operating costs decreased by 30%
This case shows that automation can solve particular production problems, make the workplace safer, and provide enormous economic benefits.
The Future of Automation in Manufacturing
The developing future of automation in manufacturing really looks good. The next advancements will encompass an even greater amount of efficiency and elasticity. Emerging trends include:
- AI-Powered Process Control: Artificial intelligence and machine learning will play an increasing role in optimizing production processes, allowing for real-time adjustments and predictive analytics.
- Predictive Maintenance: Advanced sensors and analytics will enable predictive maintenance, minimizing downtime and optimizing equipment lifecycles.
- Full Production Line Connectivity: Increased connectivity and data sharing across the entire production line will enable seamless integration and optimization of all processes.
- Real-time Quality Monitoring: Real-time quality monitoring systems will ensure consistent product quality and enable rapid response to any deviations.
Ready to Embrace the Future of Manufacturing?
If you’re ready to explore robotics and automation’s transformative potential for your manufacturing facility, contact us today. Our team of experts can help you develop a tailored automation strategy that addresses your unique needs and drives your manufacturing success.