Modern manufacture uses flexible, high-quality silicone molding. Silicone molds are used in auto, aerospace, healthcare, and consumer. This page discusses silicone molding kinds, advantages, uses, and procedures.
Molds are made by casting, compressing, or injecting silicone. The flexibility, chemical stability, heat resistance, and biocompatibility of silicone, a synthetic polymer of silicon, oxygen, carbon, and hydrogen, make it ideal for manufacturing.
Molds receive poured, crushed, or injected silicone. The silicone product is removed from the mold after curing. Silicone molding generates complicated, enduring items because to its elasticity and heat and cold resistance.
Types of Silicone Molding
Silicone molding involves compression, injection, and casting. These solutions aid projects and apps differently.
A heated mold chamber holds uncured silicone rubber in compression molding. Close the mold and push silicone into the hollow. Material hardens into molds using heat. Compression molding produces large volumes of rubber-like products with simple to fairly complex components.
For injection molding, liquid silicone is poured into a pre-formed mold under high pressure. Close the mold while silicone dries and hardens. This highly automated method is suited for high-precision applications that demand tight tolerances and constant quality. The healthcare industry, which requires accuracy and cleanliness, uses it.
Casting: Silicone is poured into a mold to cure. This method is used for prototyping and making huge, flexible, or soft pieces. It’s used in prosthetics and cinema special effects, when unique molds are needed.
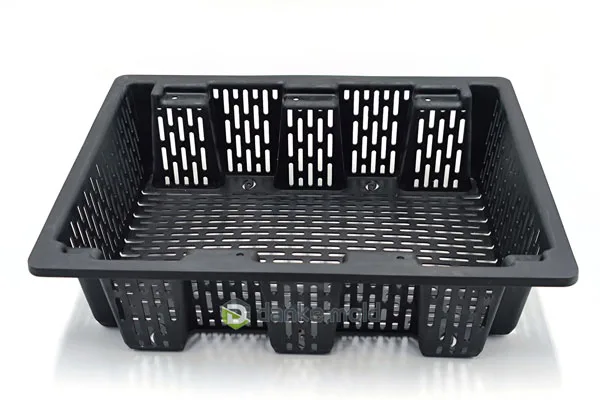
Vacuum casting baskets
Advantages of Silicone Molding
Silicone molding has several benefits over conventional production techniques because to its unique characteristics. Key advantages include:
Silicon is heat-resistant to -100°F to 500°F (-73°C to 260°C). Silicone-molded components operate well in hot or cold engines and aircraft.
Silicone resists UV, acid, and oil. Silicone molding suits harsh and corrosive conditions.
Medical implants, prosthetics, and equipment use biocompatible, non-toxic silicone. It is vital in healthcare since it does not irritate or induce allergies.
Flexible and durable: The material resists wear. Silicone molding can make complicated forms without losing strength or durability because to its flexibility.
Silicone molding produces numerous uniform components, making it cost-effective over time, even though setup is costly, particularly with injection molding.
Silicone Molding Uses
Silicone molding is used in many sectors because to its versatility and material qualities.
Implants, prostheses, catheters, pacemakers, and earplugs employ biocompatible silicone. Medical injection molding requires purity and precision.
Auto: Silicone molding creates heat-resistant engine gaskets, seals, and hoses. Its oil and chemical resistance make it perfect for cars.
Silicone molding is used for aircraft engine insulation, seals, and harsh-environment gaskets. Aerospace applications need high-pressure and temperature integrity.
Silicone molds are used to make kitchenware, electronics casings, and silicone wristbands. Silicone’s flexibility, heat resistance, and durability make it excellent for these goods.
Silicone casting is often utilized in product prototype and industrial uses. Engineers and designers may swiftly make precise molds to evaluate product functioning and aesthetics before mass manufacturing.
Conclusion
Silicone molding is a strong and adaptable manufacturing method that produces durable, flexible, and high-quality components in many sectors. The technique provides superior material characteristics, accuracy, and scalability for automotive components, medical devices, and consumer items. Silicone molding will certainly remain a staple in contemporary manufacturing, solving complicated industrial problems with trustworthy solutions.