Today’s industries employ silicone molding for its adaptability, durability, and accuracy. Complex, high-quality products are prototyped and mass-produced in silicone molds. This page discusses silicone molding, its benefits, and associated procedures.
Molding components and products using silicone rubber. Silicone is ideal for complex constructions because to its flexibility, durability, and heat resistance. Silicone molds cast excellent food, resins, metals, and plastics.
Types of Silicone Molding
Application-specific silicone molding:
- Compression Molding: Mold cavities are compressed to form silicone rubber. Mold silicone cures with heat. Large or low-precision components are commonly made this way. Bulk compression molding saves money but requires time due to manpower.
- Injection Molding: LSR is injected into a mold using high-pressure automated injection molding. The approach is perfect for mass-producing tiny, complicated things with consistent quality. Injection molding works for electronics, cars, and medical gadgets.
- Transfer Molding: Transfer molding combines injection and compression. The mold cavity receives silicone rubber from a transfer chamber. Transfer molding is better than compression molding for complex designs that need more material flow. It usually has electrical components.
- Extrusion-molded: Silicone is extruded via a die to make tubes, profiles, and seals. Although less flexible for intricate items, this approach is ideal for making consistent forms that can be trimmed to length.
The Silicone Molding Process
Though silicone molding techniques vary by kind, the following stages are typical:
1. Mold Design
The silicone molding process begins with mold design. This is usually done using 3D modeling software for accuracy. A CNC or 3D-printed master pattern is made when the design is approved.
2. Mold Making
Next, make the silicone mold. A liquid silicone mixture is poured or injected into the master pattern-created mold cavity. Depending on the silicone and curing procedure, silicone cures over many hours.
3. Casting
Curing the silicone mold lets you make many copies of the component. Pour or inject plastic, resin, or metal into the mold, let it set, then remove it.
4. De Molding
The mold is gently opened and the completed object removed once the casting substance cures. Stretchy silicone molds make it easier to release complicated structures without destroying them.
5. Post-processing
Final processing may include trimming, painting, or assembly, depending on the application. Silicone molds give flawless finishes, minimizing post-processing.
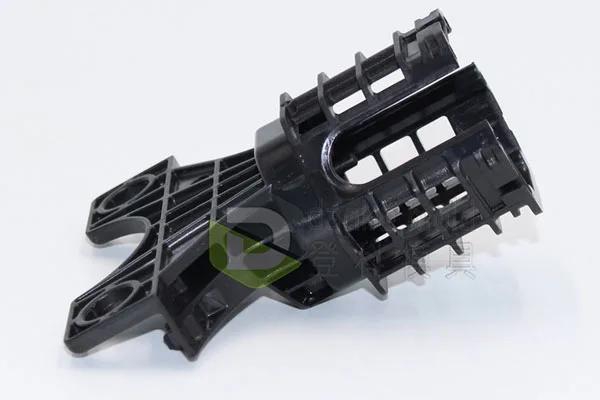
Plastic injection molding products
Silicone Molding Applications
Many industries and uses employ silicone molding:
Medical devices: Silicone molds make catheters, seals, and gaskets. Medical silicone is sterile and biocompatible.
Automotive gaskets, seals, and keypads are silicone-molded to endure high temperatures and pressures.
Silicone-molded bake, ice, wristwatch, and phone covers.
Silicone molds offer detailed components for testing and development, making them perfect for fast prototyping.
Silicone insulates electronics keypads, gaskets, and seals from heat and moisture.
Advantages of Silicone Molding
Silicone molding has several advantages:
- Durability
Silicone molds can survive numerous casting cycles without losing form or detail. This makes them perfect for mass manufacture.
- Detail and accuracy
Silicone’s elasticity and ability to capture small details make it ideal for detailed prototypes and final products.
- Temperature Resistance
Silicone can handle high and low temperatures. Automotive and electronics, whose components may be exposed to severe conditions, benefit from this.
- Reusable Molds
Reusable silicone molds make multiple item manufacture cost-effective, especially for small production runs or prototyping.
Silicone vs. Other Molding Methods
Flexibility, accuracy, and flexibility distinguish silicone molding from classical molding. Silicone molds withstand undercuts, complicated geometries, and thin walls without costly design changes, unlike metal or hard plastic molds. Silicone molding is quicker and cheaper for prototypes and small runs, whereas thermoplastic injection molding is superior for bulk.
Conclusion
Flexible, efficient, and industry-friendly silicone molding. Medical equipment and consumer goods need its complex, strong, and heat-resistant components. Technology will make silicone molding increasingly vital in innovative, high-quality product manufacture.