Injection molding, the process of creating identical plastic parts by injecting molten plastic into a mold, is a cornerstone of mass production. However, a common misconception lingers – is it truly cost-effective? Especially for startups and companies with smaller production runs, the initial investment in tooling can seem daunting.
But here’s the secret: injection molding, when used strategically, can be a powerful tool for achieving long-term cost savings and production efficiency. At Danke Mold, we possess extensive experience in injection molding, and we’re here to debunk the myth and unlock its true potential for your business.
Understanding Injection Molding Costs
Injection molding is a popular manufacturing process for producing plastic parts. While it offers numerous benefits, understanding the associated costs is crucial before embarking on an injection molding project. Here are the key factors that contribute to injection molding costs:
- Mold Design and Engineering: Mold design is a critical step in injection molding as it determines the efficiency and quality of the final product. Skilled engineers are required to design molds that optimize material flow, minimize defects, and ensure smooth production. The complexity of the part design directly impacts the mold design process, with more intricate features requiring more complex molds and higher engineering costs.
- Mold Manufacturing: The cost of mold manufacturing is closely tied to the complexity of the mold design. Simpler molds with basic shapes and features can be produced using standard manufacturing techniques at a lower cost. However, molds with intricate geometries, tight tolerances, or special features such as side actions or unscrewing mechanisms require specialized manufacturing processes and materials, resulting in higher costs.
- Material Costs: The choice of plastic material significantly influences the overall cost of injection molding. Different plastics have varying properties, performance characteristics, and price points. Commodity plastics like polypropylene (PP) and polyethylene (PE) are generally more affordable than engineering plastics such as polycarbonate (PC) or acrylonitrile butadiene styrene (ABS). Material costs can also be affected by factors such as colorants, additives, and the amount of material required per part.
- Production Volume: Production volume is crucial in determining injection molding costs. Higher production volumes typically result in lower per-unit costs due to economies of scale. The cost of tooling (mold design and manufacturing) is spread across larger parts, making it more cost-effective. However, low-volume production runs may necessitate higher per-unit costs as the tooling costs are distributed over fewer parts.
- Secondary Operations: Post-molding operations such as trimming, finishing, decorating, and assembly can contribute to the overall cost of injection molding. These secondary operations are often necessary to achieve product specifications or aesthetics. The complexity and extent of secondary operations directly impact the cost, with more involved processes requiring additional time, labor, and equipment.
- Quality Control and Testing: Ensuring the quality and consistency of injection-molded parts requires rigorous quality control measures. This includes testing and inspection procedures to identify and eliminate defects. The quality control and testing level required can influence the overall cost, with more stringent requirements typically leading to higher costs.
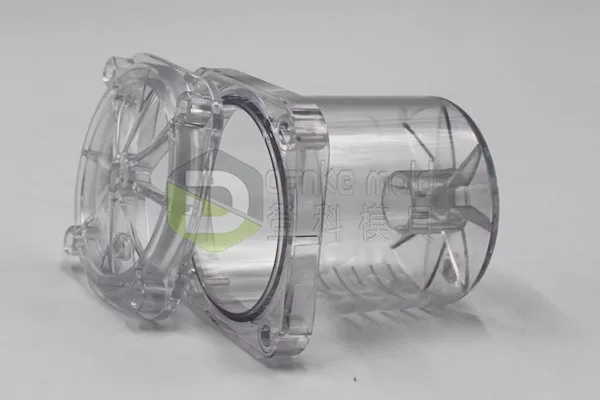
Injection molding parts
The Long-Term Advantage
While the initial investment might raise eyebrows, consider this:
- High Production Volume: Injection molding excels at creating large quantities of identical parts with exceptional consistency. This translates to significant cost savings per unit as production volume increases.
- Reduced Waste: Compared to other techniques, injection molding minimizes material waste. The leftover plastic from the sprue (the channel that feeds the molten plastic into the mold) can often be recycled and reused.
- Minimal Labor Costs: Injection molding is a highly automated process that requires minimal human intervention during production. This lowers labor costs significantly compared to manual manufacturing methods.
- Increased Speed and Efficiency: Once the mold is set up, injection molding produces parts quickly, leading to faster turnaround times and improved production efficiency.
When Does Injection Molding Make Sense?
Injection molding isn’t a one-size-fits-all solution. However, it shines under these circumstances:
- High-Volume Production: If you anticipate needing tens of thousands or even millions of identical parts, injection molding is the most cost-effective production method.
- Part Complexity: Injection molding can handle intricate geometries and features that might be challenging or expensive to produce using other methods.
- Dimensional Accuracy and Repeatability: When consistent and precise parts are critical for your application, injection molding guarantees near-perfect uniformity across every part produced.
Danke Mold: Your Partner in Cost-Effective Injection Molding
At Danke Mold, we understand that making informed manufacturing decisions is crucial for businesses of all sizes. We offer a comprehensive injection molding service, from initial design consultations to mold creation and high-volume production. We help you:
- Optimize Mold Design: Our experienced engineers ensure your mold is designed for efficient production and cost-effectiveness.
- Select the Right Materials: We will help you choose the most suitable and cost-effective plastic material for your application.
- Manage Your Production Run: Our team oversees the entire injection molding process, ensuring quality control and timely delivery.
Myth Busted: Injection Molding Can Be Cost-Effective
The initial investment in injection molding might seem like a barrier. However, when considering the long-term benefits of high-volume production, minimal waste, and reduced labor costs, injection molding emerges as a strategic choice for achieving true cost-effectiveness.
Let Danke Mold help you navigate the world of injection molding and determine if it’s the right solution for your business. Contact us today! We’ll guide you through the process, ensuring you get the most cost-effective production solution for your high-volume needs. Together, we can turn your vision into reality, one perfectly molded part at a time.