Over 300 million tons of plastic are produced globally every year, with a significant portion ending up in landfills and oceans, wreaking havoc on ecosystems. As the devastating consequences of this plastic waste become increasingly apparent, the demand for sustainable manufacturing solutions has never been higher.
Enter bioplastics—a revolutionary class of eco-friendly materials derived from renewable resources. Their versatility has found a powerful ally in injection molding, a manufacturing process undergoing a remarkable transformation. By adapting to incorporate bioplastics, injection molding is not only reshaping how we create products but is also paving the way for a greener, more sustainable future in manufacturing.
What are Bioplastics?
Injection molding, renowned for its versatility in shaping traditional plastics, has proven to be an adaptable ally in bioplastics. This manufacturing process seamlessly integrates with various bioplastic materials, requiring only minor adjustments to optimize results. These adaptations may involve modifying temperatures, pressures, and mold designs to accommodate the unique properties of each bioplastic. The success stories are already evident: compostable packaging, disposable cutlery, and medical devices are produced through bioplastic injection molding. Additionally, advancements in injection molding technology, such as improved temperature control and innovative mold materials, further enhance bioplastic production’s compatibility and efficiency.
The Rise of Bioplastics in Manufacturing
Bioplastics are steadily gaining traction across diverse sectors, from packaging to consumer goods and even the automotive industry. This growing adoption is fueled by heightened consumer awareness of environmental issues, stricter regulations on traditional plastics, and corporations setting ambitious sustainability goals. However, the widespread integration of bioplastics isn’t without challenges. Costs remain relatively high compared to conventional plastics, and some bioplastics may have performance limitations in certain applications. Additionally, the availability of bioplastics can be limited, hindering their full potential.
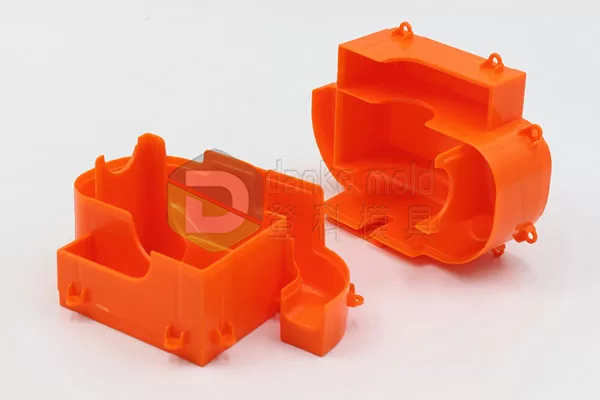
Injection molding parts
Injection Molding Adapting to Bioplastics
Despite these challenges, the injection molding industry is rising to the occasion. This adaptable manufacturing process proves its versatility by seamlessly integrating with various bioplastic materials. Minor adjustments to temperature, pressure, and mold design are often sufficient to optimize production. This adaptability has led to successful case studies, such as creating single packaging, disposable cutlery, and medical devices using bioplastic injection molding. Moreover, ongoing innovations in injection molding technology, including improved temperature control and innovative mold materials, further enhance bioplastic production’s compatibility and efficiency.
The Future of Sustainable Manufacturing
The potential of bioplastics to revolutionize manufacturing and usher in a new era of sustainability is immense. As research and development forge ahead, we can anticipate a wave of innovative bioplastic materials with enhanced properties, further expanding their applications across industries. Advancements in injection molding technology will continue to refine the production process, making it even more efficient and accessible.
However, the true power of bioplastics lies in collaboration. By fostering partnerships between material suppliers, manufacturers, designers, and consumers, we can accelerate the adoption of these sustainable alternatives. This collective effort will drive innovation, reduce costs, and create a demand for bioplastic products, ultimately minimizing the environmental impact of manufacturing.
The path toward a greener future in manufacturing is clear. With bioplastics and injection molding leading the charge, we have the world where products are not only functional, ally pleasing but also, and naturally responsible. The future of sustainable manufacturing is bright, and it is ours to shape.