A single mold type that could satisfy all of our requirements would be ideal, but this is extremely difficult to achieve: the qualities needed to produce flat pieces, like a sports plaque or medal, are different from those required to produce a piece of jewellery that will be challenging to remove from the mold because of its morphology. A number of considerations, including the metal to be cast, the part’s size, and its shape, must be made when selecting the best silicone molding for spin casting parts.
Vibrance
Silicone comes in a variety of colours, including clear, white, black, and custom hues. The user’s preferences will determine which colour silicone is used. White silicone works well for mold-making bright-coloured objects, while clear silicone is best for translucent molds. Conversely, molds for objects with dark colours are made using black silicone.
Control of Quality
Additionally, you should pick a manufacturer that is dedicated to quality control, employing stringent documentation, testing, and inspection protocols along with continual staff training to guarantee that every mold that leaves their facility satisfies their exacting standards. You will feel more at ease knowing that your molds are of the best calibre and will meet your needs.
Resistance to Temperature
The silicone’s application is determined by the temperature it can withstand without melting or degrading. A low-temperature resistant silicone would work just fine if you are creating molds for low-temperature uses, such as creating soap or candles. However, a high-temperature resistant silicone would be required if you were creating molds for high-temperature applications, such as casting metals.
Cost and Pricing
Think about the total value that the business can offer, taking into account the calibre of their products and molds, their knowledge, and their calibre of customer service.
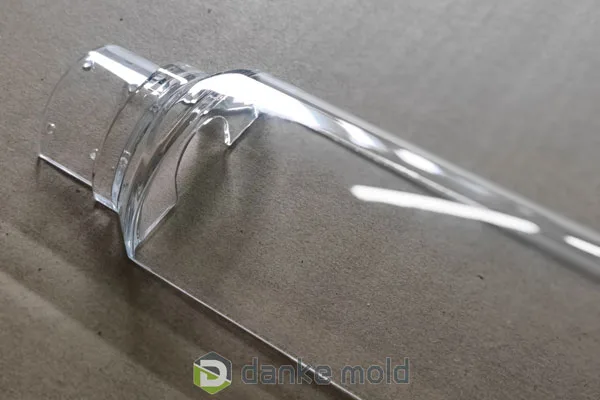
Vacuum casting products
Hardness of the Shore
The term “shore hardness” describes how stiff silicone becomes after it has cured. This feature comes in very handy when creating molds for intricately detailed products. It is simpler to keep the mold’s shape during the casting process when the silicone has a higher shore hardness. A softer silicone, on the other hand, would be easier to demold and more flexible.
The process and method of silicone molding
The most popular kind of material used in compression molding is solid silicone. The silicone molding from HTV. It also goes by the name silicone compression molding. Since the beginning of the rubber manufacturing industry, silicone compression molding has been used to mold rubber parts. After that, the mold is sealed with a top plug and compressed to ensure that the material touches every part of the mold.
Silicone substance
Silicon, hydrogen, oxygen, and carbon make up the silicone material. Food-grade silicone material satisfies FDA and EU regulations regarding food contact and safety. The silicone material is available in two shapes. Silicone rubber comes in two varieties: liquid and solid. Prior to choosing a fabrication technique, you must decide on the material for your silicone products.
Conclusion
It is imperative to allocate sufficient time to evaluate various customised silicone molds. Make sure to look up the reputations of businesses. The price will depend on the mold’s specifications. Prototypes are produced by some businesses prior to mold printing.