Injection molding is used in areas such a building, engineering, and component manufacture. Because it is adaptable, delivers high-quality finishes, and is easy to use. Moldable materials include- metals (by die-casting), glass, elastomers, and plastics (such as polymers and thermoplastics). The procedure is not new – American inventors John Wesley Hyatt and his brother, Isaac, patented it in 1872. Early goods included buttons, collar stays, and hair combs.
During World War II, the need for low-cost, mass-produced goods increased, enhancing the popularity of injection molding. Plastic is – heated and injected – into a properly designed mold to form – components for machines, moving parts, and other equipment. Engineers carefully build molds from strong metals such as aluminum or steel to withstand pressure.
- automobile components
- medical devices
- packaging
- plumbing items
- storage containers, and toys
are among the most popular applications for the products, which may vary from small machine parts to massive car body panels.
Plastic Injection Molding
Plastic injection molding offers several benefits over other materials such as glass or metal. The plastic may be molded into practically any form or size and comes in a variety of colors. It is long-lasting, sanitary, and readily available. Furthermore, certain plastics, such as thermoplastics are recyclable, making them ideal for environmentally responsible applications.
Injection Molding Process: Step by Step
The plastic injection molding process begins with-
- Raw plastic in the form of tiny pellets that are put into a hopper and heated until liquid.
- Once melted, the plastic is injected under pressure into a mold to form the desired shape.
- The pieces are then allowed to cool and solidify.
- After cooling, the mold is opened,
- And the solid plastic component is expelled by rods, plates, or air blasts.
The molds have two parts: the injection mold – which forms the plastic, and the ejector mold – which pushes the completed product out.
The method is rapid and efficient enabling for large-scale manufacture of high-quality plastic components. However, like with any manufacturing process, there may be complications, such as blistering, burn marks, or color streaks that impair the finished product. Regular maintenance and detailed examination of the plastic components assist in reducing these difficulties. Various approaches may also be employed to produce diverse looks. A two-shot or multi-shot mold – for example, blends many materials into a single component making it ideal for producing objects with soft finishes or varied colors. Insert molding is another method that involves inserting a pre-molded shape into a bigger mold and pouring molten plastic around it. This is used to connect metal pieces and plastic films to products such as food containers.
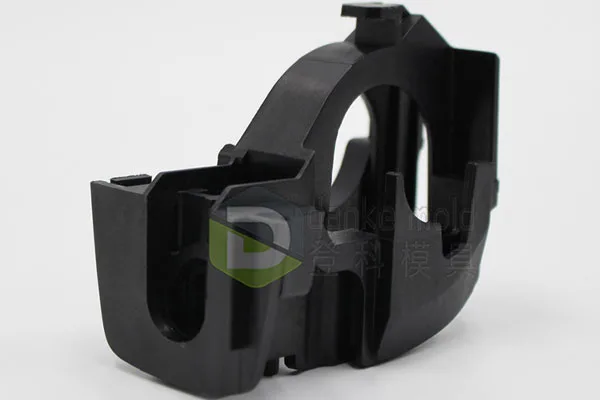
Injection molding products
Advantages and disadvantages of injection molding
The choice to employ plastic injection molding is based on the project’s unique demands. Plastic offers several advantages, including durability, flexibility, and ease of shaping.
Many thermoplastic materials are recyclable and plastic is sanitary. Thus, it is ideal for medical or food packaging. It is also resistant to extreme heat, water, and chemicals. The injection molding technique is quick and efficient, resulting in great production at minimal labor costs. It can make extremely tiny or intricate pieces – including metal inserts. But there are some downsides. The initial setup expenses for the machine and mold might be significant and developing the mold can take additional time, thereby increasing the manufacturing cost and timetable.
Smaller manufacturing runs are less cost-effective than larger ones. And the mold fabrication process limits design options. In addition, injection molding equipment needs enough room, air, and qualified workers to ensure safety. Despite these obstacles, they may be addressed at the planning stage.