A flexible tool for creative applications is silicone molds. They have a plethora of possibilities, from crafts to baking. They form elaborate cake designs as well as cupcakes and muffins. DIY enthusiasts use them to create resin, soap, and candles. Painters produce jewellery out of polymer clay, concrete planters, and other items. Jelly snacks, chocolates, and ice cubes get made with silicone molding. They are freezer-friendly, effortlessly cleaned, and non-stick. Silicone molds are tools for both cooking and crafting.
Silicone’s Use in Moulding
Let us examine the main applications of silicone molding in more detail:
Tools and Moulds:
It is perfect for producing complicated parts and components because of its qualities, which enable the creation of accurate and elaborate patterns.
Making prototypes:
During the prototype phase, silicone molds are essential because they allow precise and functional models to get created before mass manufacturing. Silicone molds allow manufacturers to test and enhance their ideas quickly and cost-effectively.
Products for Health and Medicine:
Because of its hypoallergenic qualities, endurance, and biocompatibility, silicone is a good option for these uses, which will improve patient outcomes.
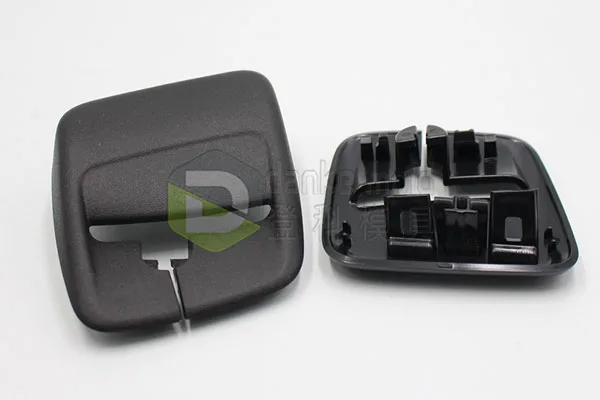
Plastic products
Design Considerations for Silicone Molds
A silicone mold gets situated atop a worktable, encircled by an apparatus for plastic injection. The mold features fine details, a robust frame, and is smooth and flexible.
It’s vital to take several things when creating a silicone mold for plastic injection to ensure the finished product fulfills your needs. We will examine material selection, mold geometry, and surface finish as the three main design factors.
Material Choice
For your plastic injection process to be successful, the material you choose for your silicone mold is essential. The silicone has got cured in platinum, tin, or room temperature vulcanization (RTV) common material used in silicone molds. The longest mold life and the highest level of durability are found in platinum-cured silicone, which makes it perfect for large-scale production runs. The least expensive but least durable silicone is RTV silicone; tin-cured silicone is more costly but has a shorter mold life.
Shape Geometry
Another crucial thing to think about is the silicone mold’s geometry. It is necessary to construct the mold in a way that permits the plastic material to cool and flow properly. The mold needs to be made the end product can get ejected.
The gate placement, parting line, and draft angle must all get considered creating the mold. It is important to position the gate like the plastic material flows through it properly. The separation line has to be crafted to reduce flash, and the draft angle to be adequate to facilitate effortless ejection of the completed item.
Level of Finish
Your silicone mold’s surface quality is crucial to ensuring the finished product lives-up to your expectations. The mold’s surface polish needs to be flawless, as it will get reflected in the final product.
The mold cavity should get polished to a mirror-like gloss to provide a perfect surface on the finished product. Malfunctions like sink marks, warping, and surface irregularities might result from inadequate mold polishing.
It’s crucial to take the material choice, mold shape, and surface polish while creating a silicone mold for plastic injection. You may ensure that the finished product fulfills your requirements and is of the highest caliber by regarding these elements.