Vacuum casting is often hailed as a champion of prototyping, enabling designers and engineers to quickly and cost-effectively create realistic models of their product concepts. However, this versatile manufacturing process offers much more than initial prototypes. While often pigeonholed as a prototyping-only tool, vacuum casting has been quietly expanding its reach into various production applications, proving its worth beyond the early stages of product development.
In this blog post, we’ll break free from the confines of the prototyping mindset and explore the innovative ways vacuum casting is being leveraged in production environments. From low-volume manufacturing to bridge production and even the creation of end-use parts, vacuum casting is proving to be a valuable asset for a wide range of industries an
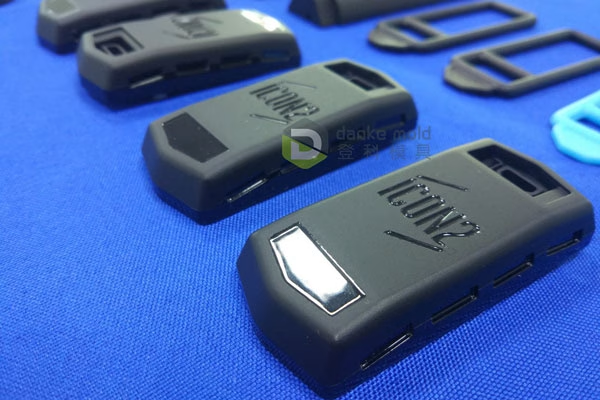
Vacuum casting parts
Vacuum Casting in Low-Volume Production
Regarding low-volume production runs, vacuum casting emerges as a cost-effective alternative to injection molding. The lower upfront costs associated with silicone mold creation make it an attractive option for projects that don’t require the mass production capabilities of injection molding. Additionally, vacuum casting boasts faster turnaround times than traditional molding methods, enabling manufacturers to quickly respond to market demands or produce customized parts with minimal lead time.
The ability to replicate intricate details and achieve a high-quality surface finish further enhances the appeal of vacuum casting for low-volume production. This makes it particularly well-suited for industries that demand precision and aesthetics.
For instance, vacuum casting is employed in the medical field to create custom prosthetics, orthotics, and implants that perfectly fit individual patients. The automotive industry leverages vacuum casting for manufacturing limited-edition or customized car parts with intricate designs. Even the consumer electronics sector utilizes this process to produce high-end audio equipment and headphones with unique aesthetic features.
Vacuum Casting for Bridge Production
Bridge production is a strategic approach where vacuum casting creates a limited number of parts while the injection molds needed for mass production are manufactured. This allows companies to introduce their product to the market sooner, gaining valuable early traction and validating demand before fully committing to large-scale production.
The benefits of using vacuum casting for bridge production are significant. It drastically reduces time-to-market, enabling companies to generate revenue and gather crucial customer feedback earlier in the product lifecycle. This feedback loop can then refine the product design and ensure its success before investing in costly injection molds. As a bridge between prototyping and mass production, vacuum casting mitigates risks and streamlines the product development process.
Vacuum Casting for End-Use Parts
While vacuum casting is often associated with prototypes, it’s important to note that the resulting parts can also serve as functional end-use products in certain scenarios. For instance, the artistic and decorative sectors frequently employ vacuum casting to create intricate sculptures, jewelry pieces, and figurines where aesthetic appeal and fine details are paramount.
In addition, functional prototypes created through vacuum casting can sometimes meet the necessary performance requirements for limited field trials or specific applications where durability isn’t a primary concern. However, it’s crucial to emphasize that the success of vacuum-cast end-use parts heavily relies on careful material selection and rigorous quality control measures to ensure their functionality and longevity.
Conclusion
Vacuum casting is a multifaceted manufacturing process that extends far beyond its traditional role in prototyping. Its versatility makes it a valuable tool for low-volume production runs, bridge manufacturing, and even creating specific end-use parts. By understanding the full potential of vacuum casting, businesses, and creators can unlock new possibilities and leverage this technique to bring their ideas to life efficiently and cost-effectively.
So, the next time you think of vacuum casting, don’t limit its potential to just prototypes – explore the broader applications and discover how it can benefit your projects beyond the initial design phase.