Vacuum casting, a unique manufacturing technology, is used for high-quality prototypes and limited production runs that may be manufactured with unsurpassed precision and complexity. Nowadays, industries seeking quick and effective manufacturing solutions turn to this approach as their preferred option.
In the mid-1900s, vacuum casting started to be used in the aerospace and automobile industries. Technology and material advancements have made the technique more widely available and effective for a greater variety of applications.
A silicone mold of the intended object is made and put inside a vacuum chamber to perform vacuum casting. After pouring liquid resin into the mold, remove all air bubbles using a suction cup to get a perfect finish.
Applications and Domains
Vacuum casting is used in many industries, including as consumer goods, automotive, medical devices, and product design. Since vacuum casting is precise and adaptable enough to be utilized for both functional prototypes and final products, it is a useful tool for product development and modification.
Advantages and Limitations
The benefits of vacuum casting are rapid prototyping, low cost of production for short runs, and precise reproduction of complex designs. However, for the greatest results, it’s important to appropriately handle concerns like material selection, mold durability, and post-processing requirements.
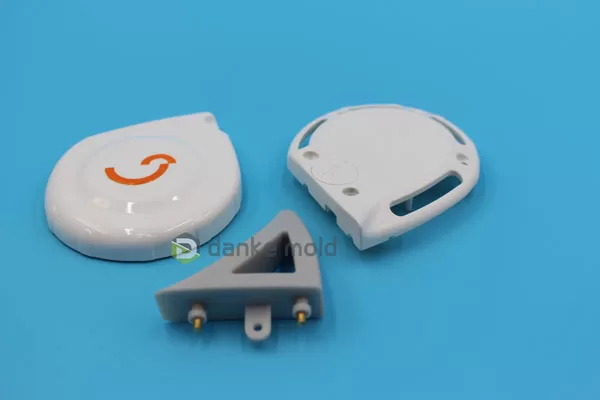
Vacuum casting products
Future Advancements and Patterns
As technology advances, the prospective uses for vacuum casting become increasingly interesting. Technological developments in material science, automation, and digital integration may improve the process even more, increasing its efficacy and expanding the range of applications for vacuum casting.
For the best quality and longevity in small batches of practical plastic parts, vacuum casting is the perfect technique. Using a mold of the desired item, liquid plastic is poured into the mold, and any air bubbles are then removed by placing the mold in a vacuum chamber. A portion with flawless mechanical qualities and no flaws is the end product. All things considered, vacuum casting is an economical and effective method of producing high-quality plastic parts for a range of uses.
Additionally, a variety of materials, including rubber-like materials and stiff and flexible polymers, can be employed in vacuum casting. Because of its adaptability, it is a preferred option for the consumer products, automotive, and aerospace industries. Additionally, vacuum casting is a preferred method for small-scale production and prototyping due to its ability to produce precise and detailed parts with constant quality. Additionally, the technique is easily scaled up for larger production runs, which gives producers a flexible way to fulfill different levels of demand.
Furthermore, complicated shapes and complex geometries that can be challenging to obtain with other production techniques can be created with vacuum casting. Because of its adaptability, it is a well-liked option for sectors that need premium, customized parts. Because it does not require costly molds or tooling, the technique is also an affordable option for making small batches of parts. Additionally, vacuum casting is a flexible alternative for a wide range of applications since it can be utilized to make parts with variable degrees of flexibility, hardness, and surface treatments.
In conclusion, vacuum casting is an extremely versatile and trustworthy manufacturing method that offers unmatched precision and quality for a variety of industries. Its ability to manufacture complex objects with exceptional accuracy makes it a vital tool in the realm of modern manufacturing.