In rapid prototyping, where speed and precision intersect, vacuum casting stands out as a technique that can replicate intricate details and surface finishes with unparalleled accuracy. This process has become the go-to choice for designers and engineers seeking prototypes that closely mimic the look, feel, and functionality of final products.
The Art of Vacuum Casting
At its core, vacuum casting is a casting process that utilizes a vacuum to draw liquid material into a mold. This method ensures the absence of air bubbles, which can compromise the integrity of the final part and allows for exceptional levels of detail replication. The process typically begins with creating a master pattern, often using 3D printing or CNC machining. A silicone mold is crafted from this pattern, capable of capturing even the most minute nuances of the original design.
Once the mold is prepared, the chosen material, typically a polyurethane resin, is mixed and poured into the mold chamber. The chamber is then evacuated, creating a vacuum that draws the resin into every crevice of the mold. The resin is allowed to cure, and upon removal from the mold, the finished part exhibits the intricate details and surface finishes that set vacuum casting apart.
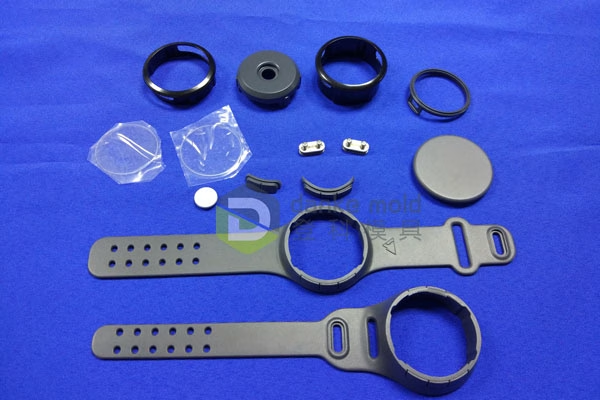
Silicone watch bands
Hyper-Realistic Prototyping
The pursuit of hyper-realistic prototyping is driven by the desire to create prototypes that look like the final product and perform similarly. Vacuum casting excels in this regard, offering several key advantages:
- Unmatched Detail Replication: The vacuum casting process and high-quality silicone molds ensure the faithful replication of even the most intricate design features. From fine textures to sharp edges, vacuum casting captures it all.
- Exceptional Surface Finishes: The absence of air bubbles and the use of advanced resins allow for creating prototypes with smooth, flawless surfaces. To achieve a hyper-realistic appearance, these surfaces can be further enhanced through various finishing techniques, including painting, polishing, and plating.
- Material Versatility: It offers various resins with varying properties, including rigidity, flexibility, and transparency. This wide range of options empowers designers and engineers to create prototypes that closely mimic the material characteristics of the final product.
- Functional Prototyping: Beyond aesthetics, vacuum casting also enables the creation of functional prototypes. The chosen resins can exhibit mechanical properties that allow for testing of fit, form, and function, providing valuable insights into the final product’s performance.
Advanced Materials and Techniques
Advancements further aid the pursuit of hyper-realism in vacuum casting materials and techniques. High-performance resins capable of replicating a wide range of material properties are now available. Overmolding and insert molding allow for integrating multiple materials and components into a single prototype, further enhancing its realism.
Vacuum Casting: A Gateway to Hyper-Realistic Prototyping
In the world of product development, where the line between prototype and final product is constantly blurred, vacuum casting is a testament to the power of advanced manufacturing techniques. Its ability to create hyper-realistic prototypes with unmatched detail and surface finishes has revolutionized how designers and engineers bring their ideas to life.
Are you ready to take your prototyping to the next level? Partner with Danke Mold, a leading manufacturing company offering outsourced vacuum casting services. Our expertise and commitment to quality ensure that your prototypes achieve the highest levels of detail and surface finish.