The choice of the right manufacturing process is pivotal to bringing your product vision to life. Whether you’re developing a prototype or gearing up for mass production, deciding between vacuum casting and injection molding for plastic parts can significantly impact your project’s timeline, budget, and overall success.
Vacuum casting and injection molding are both effective methods for producing high-quality plastic parts, but they differ significantly in terms of cost, speed, material options, production volume capabilities, and the level of complexity they can handle.
In this blog post, we’ll compare these two processes in detail, examining their pros and cons across various key factors. By understanding the nuances of vacuum casting and injection molding, you can decide which process fits your specific project requirements.
Head-to-Head Comparison
Cost:
- Vacuum Casting: One of the major advantages of vacuum casting is its lower upfront costs. The silicone molds used in this process are significantly less expensive than the steel or aluminum molds required for injection molding. However, the cost per part is typically higher due to the manual labor involved in casting, de-molding, and finishing each piece.
- Injection Molding: While injection molding demands a higher initial investment for tooling, the cost per part drops dramatically as production volume increases. This is because the expensive molds can produce thousands or even millions of parts.
Comparison: If your project requires a small to medium number of parts, vacuum casting is likely the more cost-effective option. However, for large-scale production, injection molding becomes increasingly economical as the tooling cost is spread across a larger number of units.
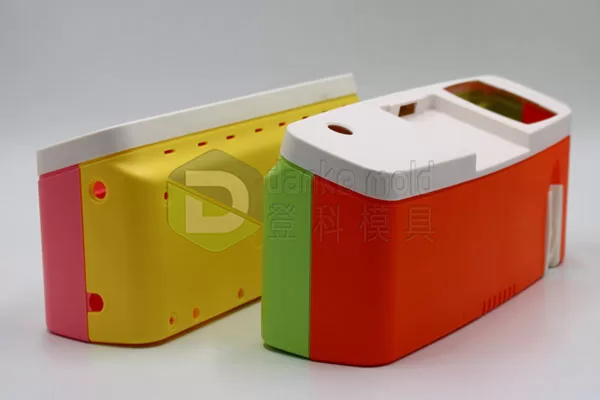
Injection molding molds
Speed:
- Vacuum Casting: Vacuum casting offers a relatively quick turnaround time, especially for prototypes and small batches. Each part can be cast and cured within hours, allowing for faster iteration and testing.
- Injection Molding: The initial lead time for injection molding can be longer due to the complexity of designing and manufacturing the molds. However, once the mold is ready, the production speed is extremely fast, with cycle times often measured in seconds or minutes.
Comparison: If speed is critical for your initial prototypes or small-batch production, vacuum casting is the clear winner. However, for high-volume production where time-to-market is less crucial than per-part production speed, injection molding’s rapid cycle times make it the superior choice.
Material Options:
- Vacuum Casting: While vacuum casting offers a range of polyurethane resins with properties that mimic various thermoplastics, the material options are more limited than injection molding.
- Injection Molding: This process allows for a vast selection of thermoplastics and some thermosetting polymers, providing greater flexibility to choose the material that best suits your product’s specific requirements.
Comparison: If your project demands a wide range of material properties or specific engineering-grade plastics, injection molding is the more versatile.
Production Volume:
- Vacuum Casting: Ideal for prototyping, low-volume production runs (typically up to a few hundred parts), and bridge production (transitioning from prototypes to injection molded parts).
- Injection Molding: The optimal choice for medium to high-volume production, where the large number of parts produced justifies the initial tooling investment.
Comparison: Vacuum casting is a suitable option if you need a few parts or are still in the prototyping phase. However, for mass production, injection molding is the more efficient and cost-effective method.
Part Complexity and Detail:
- Vacuum Casting: While it can produce parts with good detail and complexity, it might struggle with extremely intricate features, undercuts, or parts with very tight tolerances.
- Injection Molding: This process excels at producing parts with high levels of detail, complex geometries, and tight tolerances. Undercuts and internal features can be easily achieved through side actions or other tooling mechanisms.
Comparison: Vacuum casting suffices for simpler parts or those with moderate complexity. However, if your product demands intricate details, complex geometries, or tight tolerances, injection molding is preferred.
Conclusion
In summary, vacuum casting and injection molding are valuable manufacturing processes, each with distinct advantages and limitations. Vacuum casting shines in its affordability for smaller production runs and its rapid turnaround time, making it ideal for prototyping and low-volume manufacturing. Injection molding, on the other hand, excel in high-volume production, offering lower per-part costs, a wider range of material options, and the ability to create highly complex and detailed parts.
Ultimately, the best choice for your project boils down to your specific requirements. Consider factors like your budget, timeline, desired materials, production volume, and the complexity of your part design. By carefully weighing the pros and cons of vacuum casting and injection molding, you’ll be well-equipped to make an informed decision that aligns with your project goals and ensures a successful outcome.
Remember, there’s no one-size-fits-all answer. Take the time to assess your needs, consult with experts if necessary, and choose the process that best brings your vision to life.