Compression Molding
-
Silicone Rubber Parts
-
Polyurethane Parts
-
No MOQ Request
-
Cost Effective Tooling
What is Compression Molding
Compression molding is a manufacturing process used to shape materials like silicone, rubber and thermosetting polymers by using compressive force to squeeze them with a two-part mold, consisting of an upper and lower section. It’s the heat and pressure that allows solid materials to soften and reform into new structures that are wholly even and cured.
Compression molding is a versatile and cost-effective manufacturing process that is widely used in the production of high-quality parts across multiple industries. Whether it’s rubber, silicone, or thermosetting plastics, the benefits of compression molding, including its precision, flexibility with materials, and energy efficiency, make it an ideal choice for manufacturing durable components.
Although originally innovated for synthetic materials, compression molding remains the most economical method for processing thermosetting plastics. In contrast, injection molding is generally favored for thermoplastics.
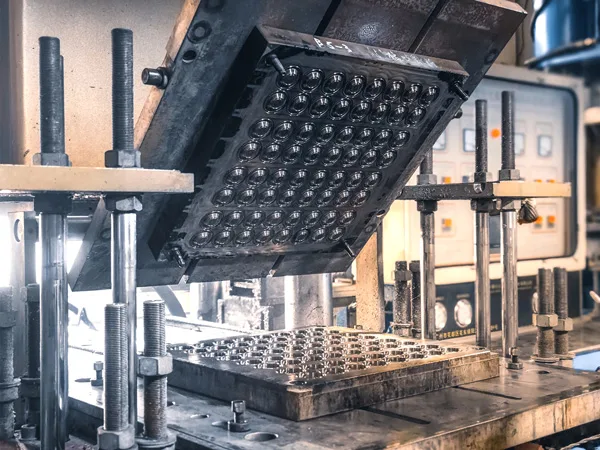
How Compression Molding Works
Step 1: Create the mold, which is responsible for shaping the end product. Set it on the compression molding machine.
Step 2: Clean the mold thoroughly and apply release agent on it.
Step 3: Place a pre-measured amount of material into the open mold cavity.
Step 4: The mold is closed, and heat & pressure are applied, causing the material to soften and flow to fill the mold.
Step 5: Curing/Solidification – The material is held under pressure until it cures.
Step 6: Once the shapes are complete, the mold is opened. Take the finished part out of the mold, remove the flashes or extra edges.
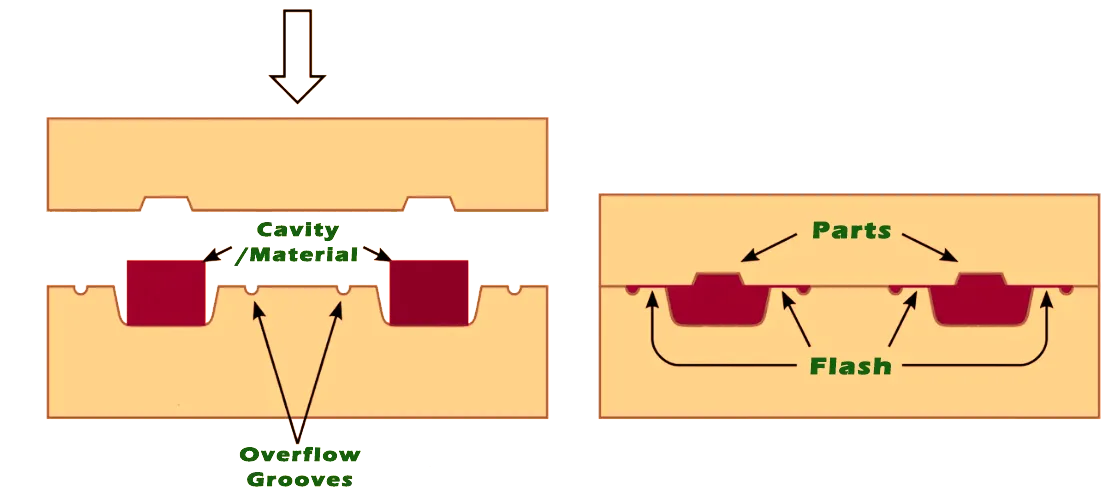
Advantages of Compression Molding
1. The tooling cost is lower. Compression mold has less infrastructure requirements than tools designed for other molding methods (like injection molding). Tools can be made of aluminum or lower grades of steel which can reduce costs
2. Cost-effective for medium to high production runs. It’s an economical method of process for volume manufacturing due to the lower tooling cost.
3. The process is ideal for making parts that are intended to undergo high levels of usage and stress. It is great for producing thicker parts and larger, bulky items with uniform dimensions.
Limitation of Compression Molding
1. Longer Cycle Times: Compared to injection molding, compression mold need longer cycle times to solidify the materials (Cure in the mold), which can impact overall production speed.
2. More material waste: Compression mold is not as precise as injection mold, so the mold cavity has to be overfilled to achieve the correct pressure to cure the part. Moreover, It is necessary to squeeze air out of the cavity by using excess material to create a void-free part, which again increases wastage, so the material waste is often more than injection molding. Waste thermoset rubber or plastic generally cannot be melted down and reused.
3. Limited complexity for some product designs: compression mold usually prefers larger, simpler products, because the limited flow of material within the cavity often makes the elimination of voids, air traps and knit lines difficult when trying to produce more intricate parts
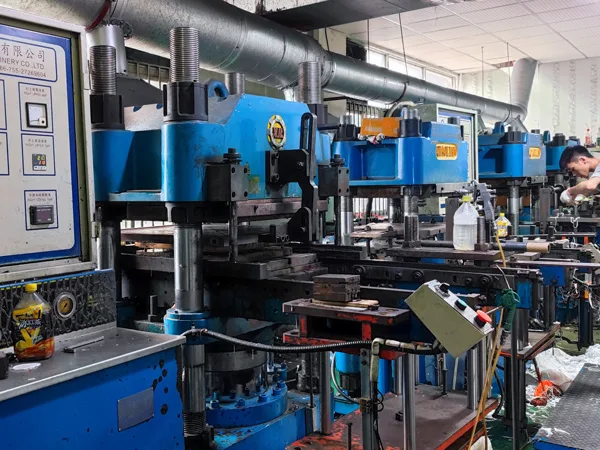
The Applications of Compression Molding
1. Rubber Parts/Silicone parts: Compression molding is commonly used to produce rubber parts, such as seals, gaskets, and hoses. And silicone parts which has ability to handle high temperatures and provide excellent flexibility makes it perfect for medical devices, seals, and cookware.
2. Vehicle parts: automobile parts including bumpers, door seals, and weather stripping, are produced using compression molding. The process offers the durability and precision required for such critical components.
3. Kitchenware: many kitchen tools, utensils, and appliances have parts that are compression molded. Dinnerware, including bowls, cups, plates, and more, especially those made out of melamine, is often manufactured using compression molding.
4. Medical Devices- Silicone compression molding is widely used for medical parts such as catheters, seals, and prosthetics. The process ensures that these components meet stringent regulatory requirements while maintaining high precision.
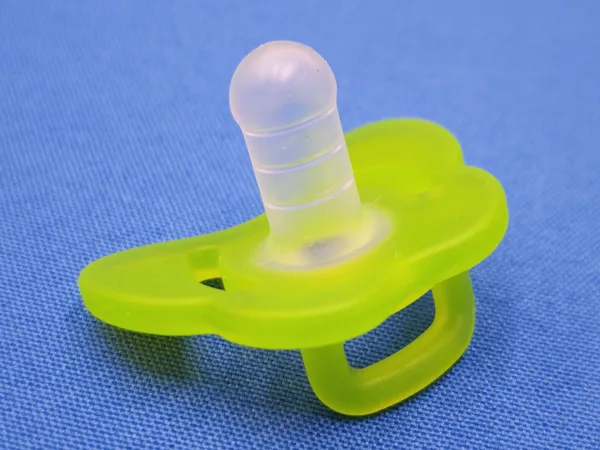
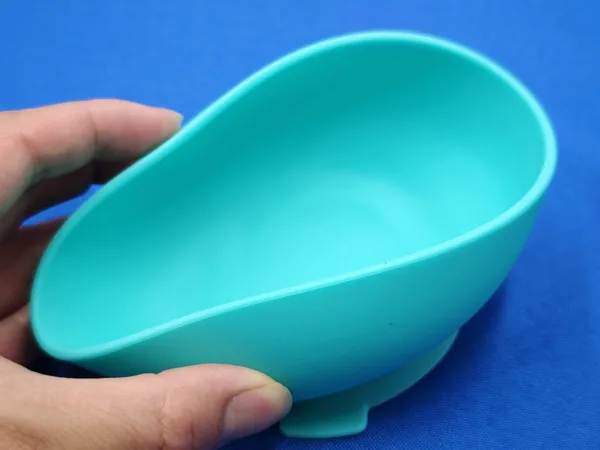
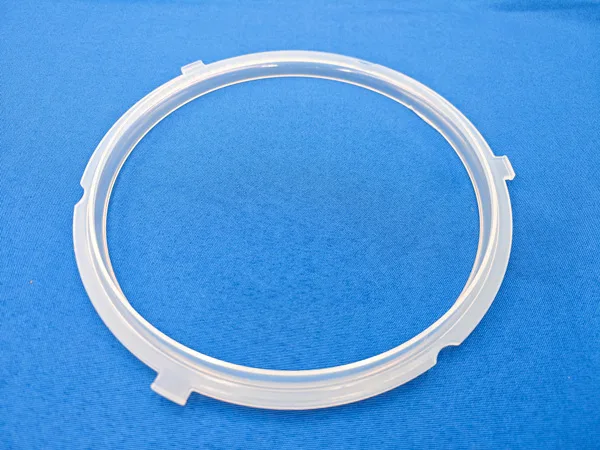
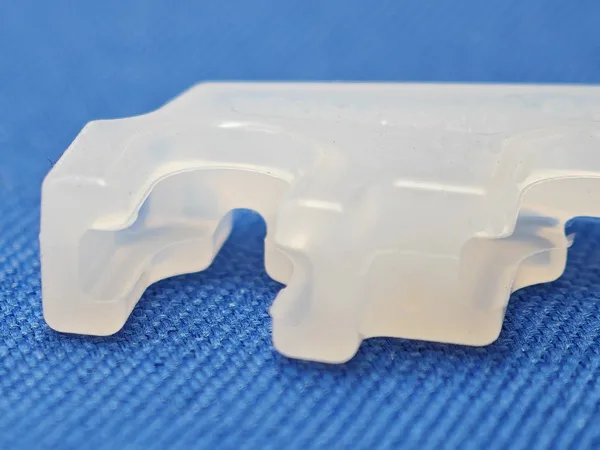
Are you looking for a reliable compression molding manufacturer with competitive price for the high-quality silicone production?